Bio-containment and/or segregation are some of the most valuable components of biosafety. These protocols are established to prevent potential exposure to infectious agents and to contain possible exposure as quickly as possible, as close as possible to the index case. The component that makes infectious agents more mobile today in pig production systems is transportation. Pig operations use daily transport not only for the movement of people and the delivery of feed, but also for the continuous movement of animals. In this first article of a series, we will review the different challenges we need to overcome in order to achieve more efficient biosecurity in pig transport vehicles.
The first challenge to achieving a completely clean surface is the presence of biofilm. Biofilm is made of a secretion of extracellular polymers and microorganisms that accumulate on inert surfaces (Photo 1). This occurs in animal production environments, for example, due to the accumulation of secretions over time, and can be made worse by the type of organic matter and the mineral profile content of the water used. Biofilm acts as a mechanical barrier that decreases the effectiveness of disinfectants. Acid detergents can penetrate the biofilm, making the surface more susceptible to disinfectants, and making the process more effective, as disinfectant is being applied to a surface that has been previously removed of any scale and biofilm.
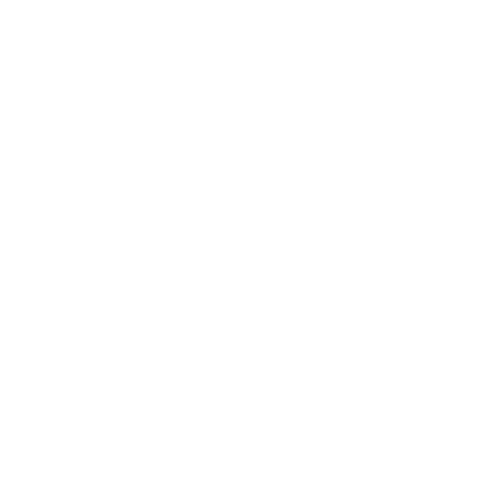
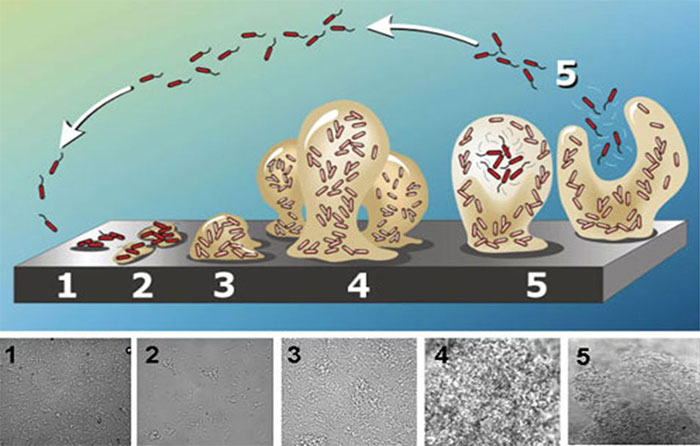
Photo 1. Schematic representation of biofilm formation. From bacterial attachment to the surface, to mature biofilm formation formed of polysaccharide. "Mushroom" shape prior to detachment. Source: Abraham Adu-Gyamfi
The second challenge is organic matter, which together with the biofilm could become the substrate for bacteria growth and for the development of different microbiological challenges. Hinges and corners of equipment and vehicles hold onto residual organic matter and even more so during the winter time, where ice residuals could carry thousands of viral particles such as PRRS, PED and ASF viruses that are very resistant to very low temperatures. The accumulation of the biofilm is a critical factor, since it limits the effectiveness of disinfectants on organisms on the surfaces. Microorganisms use these biofilms as a shield and housing structure to remain on the surfaces continuing to affect the surface that you thought you had cleaned.
The third challenge has to do with the porosity of surface to be cleaned. The ideal surface is stainless steel, but aluminum could also be conducive to cleaning processes. On the other hand however, the presence of wood or other similar highly porous materials represents a challenge to removing the organic matter and biofilms. It is easier to clean surfaces with little or no porosity. In the case of more porous surfaces, we must try to compensate with mechanical action and/or pressure for a better incorporation of the detergent into the surface (Photo 2).
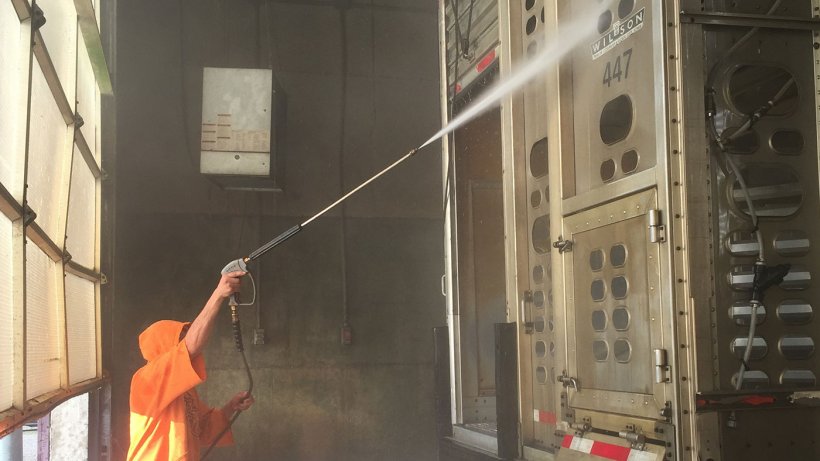
Photo 2. Power washing of a truck exterior.
The fourth challenge is water quality and its chemical and microbiological content. High mineral content, such as manganese, iron, calcium, as well as pH ranges and salt deposits could interfere negatively with the chemistry of the disinfectant, as well as serve as a substrate for bacteria. Hard water could facilitate scale formation that gradually could become more visible with a change in color of the aluminum surfaces. Some bacteria grow better in environments with high iron, manganese and mineral contents that facilitate their establishment and permanence on a surface, especially with those that have favorable porosity conditions.
The fifth challenge is the timing and movements of the workflow system. This timing represents a critical challenge at the trailer wash unit because if it is not done properly, the dry cleaning (first step that removes the organic matter) could overlap with the use of pressure water, potentially cross contaminating other areas due to the generation of organic aerosols. Surfaces must be dry before using the disinfectant which could be compromised due to poor timing, and finally, the trailers could leave the facility without having time to dry, after the disinfectant been used, or even worse, under rainy weather conditions, over-diluting and washing out the disinfectant.
The sixth challenge is consistency; the quality and maintenance of the equipment for the product application: Water pressure and water heaters. Is the right equipment being used? Do you have the correct pressure? Right temperature range? Foaming quality achieved? Coverage and dilution should be evaluated and adjusted when necessary. In addition to using the right product, we need to have appropriate and efficient delivery equipment.