Introduction
The finishing unit is meant to accommodate the pig’s needs after it has undergone the first difficult weeks after weaning. Normally, the finishing period starts when the live weight reaches 20-35 kg equivalent to an age of 10-13 weeks. The finishing period varies among countries and depends on the trading pattern and the slaughter weight. However, regardless of this the finishing unit should provide a comfortable environment, which provides optimal conditions for a high growth rate and a high feed conversion rate. Frequently, the finishing unit receives too low attention both when it is designed and subsequently managed. As a result production suffers.
Finishing unit – considerations
As for the weaning unit the finishing unit should be designed for all in all out management to allow cleaning and disinfection between batches and close control of the environment.
The number of finisher rooms depends on the projected average daily gain and expected live weight when pigs are entering the unit and the slaughter weight. Since the finisher period is somewhat longer than the weaner period it may be more difficult to project the number of rooms that is required. Thus, if the design of the unit is based on a high average daily gain there may not be sufficient time to finish all pigs in time before the next batch of weaners is due to arrive.
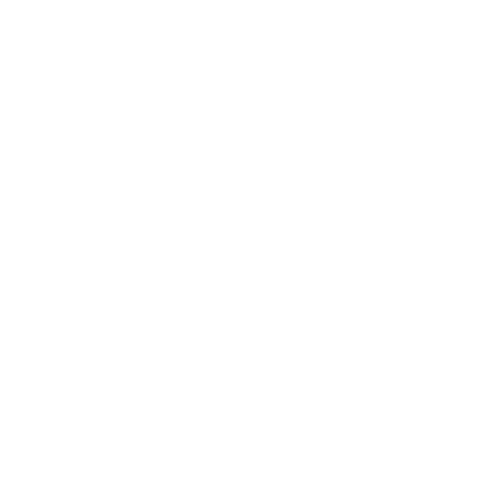
Moreover, it is important to consider the strategy for delivery of pigs. Since pigs’ growth rate differ they will not all be ready for slaughter at the same time. If the normal live weight at slaughter is 100 kg the average weight of the pigs in a room will be around 80 kg when the first animals are ready for slaughter, while the smallest weigh 60 kg only.
High temperatures and disease may slow down the growth rate considerably and increase the weight variation. The effects are illustrated in Figures 1 and 2. The first diagram shows the weight distribution of pigs with a high growth rate and low weight variation (standard deviation of 6 kg) meaning that they have not been particularly affected by environment or health. The second diagram shows the weight distribution of a group of pigs with a low growth rate and a high weight variation (standard deviation of 10 kg). Comparison of the two figures indicates that it takes longer time to empty a room when weight variation is high.
Figure 1. Weight distribution of a group pigs with a high growth rate and low weight variation (sd=6 kg) when the first pigs are due for slaughter at 100 kg.
Figure 2. Weight distribution of a group pigs with a low growth rate and high weight variation (sd=10 kg) when the first pigs are due for slaughter at 100 kg.
Table 1. Typical design criteria of a finishing unit for pigs delivered at 100 kg.
Weight at transfer | ||
---|---|---|
20 kg | 30 kg | |
Number of deliveries | 3 | 3 |
Days in unit | 102 | 88 |
Days for cleaning | 3 | 3 |
Space per pig, m2 | 0,65 | 0,65 |
Ventilation, m3/hr* | 15-140 | 15-140 |
Relative humidity, % | 50-70 | 50-70 |
Temperature, start** | 24 | 22 |
Temperature, end** | 16 | 16 |
*Ventilation rate depends on climate – the lowest rate should be applied in a temperate climate like the Danish – while the rate should be increased in a warmer one such as the Spanish. **Heating is required in areas with low temperatures during winter, while cooling is a necessity to offset the negative effects of high temperatures during the warm period. |
Pen design
Danish studies indicate that pen shape should be rectangular with a 2:1 length:width ratio as for the weaner pen, which accommodates activities such as resting, eating, defecating as well as social activities. Considering that the length of a pig at slaughter at 100 kg is about 130 cm – the pen width should be at least 2.2 m wide to accommodate pig behaviour. Danish pens are typically 2.2 – 2.6 m wide and 4.5-6.0 m deep regardless of feeding system.
Trials have shown that a group size of 15-25 pigs per pen is ideal and it also coincides with the capacity of most feeders on the market. An extra water source apart from that supplied via the feeder should be provided.
Slats should be concrete with a slat width of 80-90 mm and a slot width of 18 mm, which is also the maximum slot width according to EU legislation. Preferably, slats should always be installed in such a way that pigs are allowed to stand parallel with the beams while eating, since this reduces leg injuries.
For dry feeding systems the feeder should be placed at about one third of the length of the pen closest to the walkway, since this provides the best space distribution for eating, defecating and resting.
Figure 1. Pen with dry feeding – closed pen partition in the resting area and open pen partition in the dunging area, which facilitate defecation.
For liquid feeding systems the pen length is determined by the number of pigs that can eat simultaneously shoulder by shoulder. The shoulder width of the pigs slaughtered at 100 kg is 32 cm, which means that a pen for 15 pigs must have a length of 4.8 m.
Figure 2. Pens for liquid feeding must allow all pigs to eat simultaneously.
Figure 3. Pens with automatic weighing systems for large groups of pigs have greater fall-out, are more difficult to manage and performance is poorer than for more traditional pen designs for smaller groups.