While a previous article focussed on using feed ingredients that have originated from a biosecure source and have been delivered to the feed mill in a biosecure way, this final article will focus on the biosecure reception, storage, and processing of these ingredients at the feed mill and the biosecure delivery of final feed.
The manufacturing stage of the feed supply chain – Feed mill biosecurity
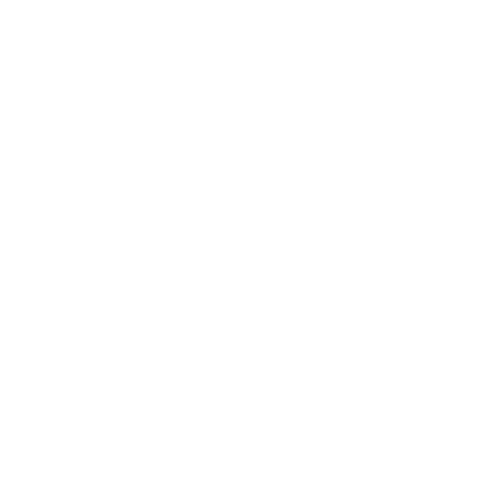
Solid and liquid feed ingredients arrive in both small to medium sized containers (e.g. bags, totes, pails, and barrels) and in larger mobile containers (e.g. trailers, train cars, and other types of containers) and how these ingredients are received, stored and handled can vary dramatically from feed mill to feed mill. Therefore, each feed mill requires customized biosecurity protocols.
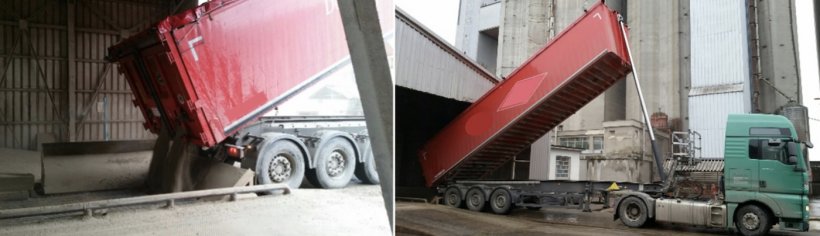
Ingredient reception
The biosecure reception of solid and liquid ingredients into the milling system is the most critical consideration to prevent the contamination of feed ingredients with infectious pathogens. Care must be taken to ensure that the transfer of the ingredients into the ingredient handling, storage, and mixing equipment is not susceptible to cross contamination.
A few practical and common protocols include the following:
- Traffic Controls – the movement of people and vehicles should be controlled in a way that considers and minimizes the risk of gross organic contamination of the site and, ultimately, the ingredients. The most likely route of contamination is the exposure of bulk intake points to vehicles returning from potentially infected pig production sites. Ideally, bulk ingredient delivery traffic should be separate from potentially contaminated traffic (e.g. delivery vehicles returning from farms or customer vehicle traffic).
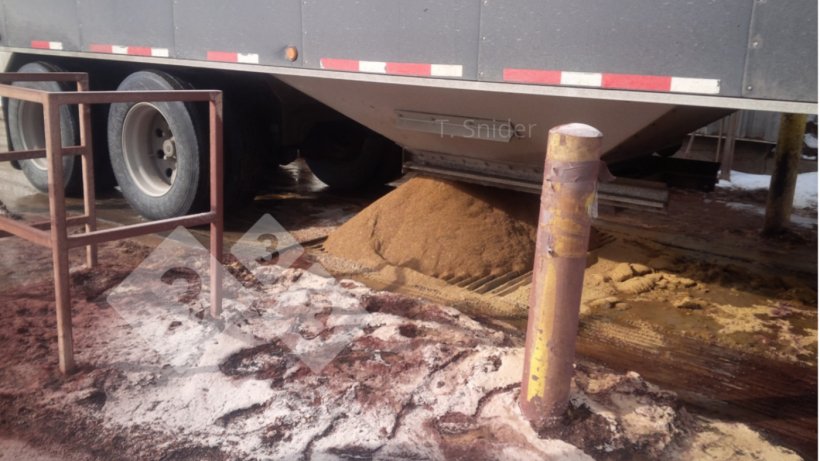
- Reception Controls - Upon arrival, the external packaging of ingredients and the vehicles that deliver these ingredients should be visually inspected to ensure the absence of obvious contamination with organic material. Prior to ingredient off-loading, the removal of any obvious contamination from vehicles (e.g. mud and snow from vehicle undercarriage and ‘mud flaps’) should occur.
- Product Handling Controls – As bulk and bagged ingredients enter the mill’s ingredient handling equipment the transfer should occur in a biosecure manner (Image 1). It is critical to utilize clean and dedicated intake reception equipment (e.g. bulk or bag reception hoppers) to minimize the risk of ingredient contamination. Preventing the overflow of ingredients around the intake points and disallowing the sweeping of excess overflow material into the intake point (Image 2) are critical steps and ingredient intake points should be covered when not in use (Image 3).
Image 3. Examples of systems that protect ingredient intake locations from contamination when not in use. North America and Europe.
Storage
Before ingredients are used to make feed, biosecure storage should occur. Bulk ingredients should be stored in enclosed containers (i.e. bins and tanks) and not in open bunkers that are exposed to contamination by vehicle traffic and animals. Storage of ingredients delivered in bags and containers should occur in a secure warehouse on pallets or shelving to prevent access by rodents and birds and away from liquid contamination.
Processing
After the complete feed has been prepared and before it is delivered or consumed, additional processing like pelleting, chemical treatments (e.g. formaldehyde), and applying an inventory period at a minimum storage temperature are options that have proven to be effective at preventing the survival of infectious pathogens that may have contaminated the feed.
The post-manufacturing stage of the feed supply chain – Feed delivery biosecurity
The final step before consumption is the delivery from the feed mill to the pig production facility. Although most of the feed is delivered in a bulk form, a significant amount of feed is delivered in bags so the biosecure delivery of both forms must be considered.
It is important to ensure that the bulk handling area inside of the delivery vehicle is clean and that dirty footwear and equipment do not gain access. Reviewing this basic concept for each feed mill is critical.
Commercial bulk feed delivery vehicles commonly move between the feed mill and several production sites on the same day and within the same week. Therefore, the external contamination of these trucks presents a clear risk of cross contamination at the mill that they return to and the production sites they visit. Taking steps to organize biosecure deliveries is critical and may include scheduling deliveries in order of health status, designating delivery vehicles to specific productions flows, and incorporating strategic vehicle decontamination to protect both the mill and the farms being served. Like any visitor to a production site, feed delivery drivers are routinely asked to use footwear covers and to never cross clean line boundaries.
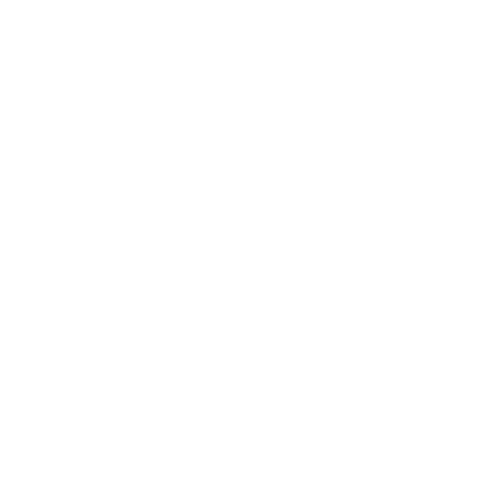
Whenever bagged feed is delivered to a production site it should be delivered on a pallet and the bags should be properly protected from contamination with a plastic wrap to avoid external contamination of the bags.
Conclusion
Although disease transmission through the feed supply chain is an event that is likely to happen infrequently under normal conditions, the impact of a single transmission event can have a catastrophic impact on the viability of an individual production site or, indeed, a national industry. Therefore understanding and applying some basic biosecurity concepts to the feed supply chain should be a priority.