Feed efficiency as it is measured by the feed conversion ratio (FCR) is basically an engineering concept. It is the amount of feed which “disappears” from a production site divided by the weight increase produced in the animals to which it is delivered. Notice that I did not say “fed” anywhere. We have not the foggiest idea how much pigs actually eat in commercial settings so the right thing to do is measure what is delivered and dumped vs what is vacuumed and removed, if any at the end. There is a lot of that which never reaches a pigs stomach.
In addition, there are a lot of misconceptions about feed efficiency and even more surrounding the economics associated with it. Some producers and consultants place a monetary value on a change in the FCR, usually the value of a “point” (a hundredth) or a “tenth”. This is perceived to be the “cost savings” associated with improving (or deteriorating) the FCR by this amount. In this first article we will examine some of the problems with the measure itself and then next time, we will look at the economics of FCR so you are never fooling yourself with what can be a very valuable measure.
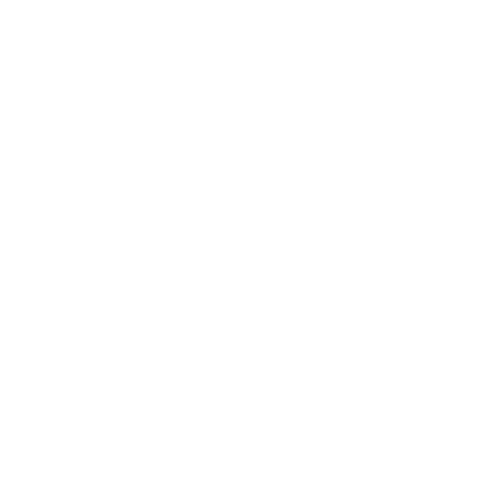
Let’s begin with the fact that producers don’t really measure any part of the inputs needed to calculate the FCR very well, and especially not down to the hundredths place. It’s a classic case of being “precisely inaccurate”. The feed weight which is part of the equation is that which was supposedly delivered to the barn where the animals were growing. A lot of things can cause these numbers to be off including leftover feed which was not cleaned from the previous group and feed remaining stuck in bins at the end of the turn. On the weight side, almost no U.S. producer ever individually weighs their animals at any time on the farm. They wait to get the kill sheet back from the packer to know the total weight marketed. Most packers do not weigh the live animals, they weigh the hot carcasses and convert them to live weights with a plant standard yield. Some weigh the animals in the truck and then the truck when it is emptied to calculate a total plant weight delivered.
For the typical producer, payment is made on the basis of the carcass weight, which is the most accurately weighed of all the FCR components. However, a recent survey of U.S. producers showed that only 17% calculate the FCR for the carcass. The rest use the standard FCR of live weight to benchmark their farm and finishing performance. It is much more revealing and accurate to make the transition to the carcass FCR since this is the real product of the farm and the use of some feed materials, such as distillery by-products can significantly change the yield of the live animal when certain threshold levels or more are fed.
We know that every animal in the barn has its own individual FCR but current production technologies do not allow us to measure individual animal consumption and weight (except in the sow herd). So the measure we use is the average of the closeout group. Unfortunately, as I have pointed out before, this number cannot be given to us when there is time to notice a problem or take any action to correct things as it is not available until the animals are sold and harvested.
The classic problem of benchmarking FCR either across your own barns or between your farm and others in a database is the problem of “holding all else constant”. When you change something in a biological system, rarely is everything else held constant but rarely do we acknowledge this when the comparisons begin. The effects which cause the difference also spill into other effects sometimes throughout the system and often in ways that are not easily traced so that a full accounting can be used to compare.
So when you hear that reducing micron size on feed ingredients like corn, for instance, can improve FCR, you should also remember that on some farms, reducing micron size below a threshold level leads to increased ulcers in late stage finishing pigs, sudden death of some of those pigs (and therefore increased mortality rate) which is usually not part of the benchmark comparison of FCR. As feed becomes finer, bridging can occur in feed bins and systems where the powdery feed clings to the sides of bins and clogs feed lines. These events can lead to feed-out events (impacting average daily gain, mortality and finished weight), which is not usually part of the benchmark comparison of FCR. In addition, residue issues in animals may increase when certain medications are in the feed which is “stuck” to the insides of the bin and augur systems and then falls into the next load of feed which is then “delivered” in the feed at a time too close to harvest to be allowed by regulations or some export market qualifications. You get the picture. In general, when you do hold all things constant, improving FCR can be, but is not always, associated with increased mortality, slower average growth, quality issues (too lean, which is now being discouraged by some major packers) and equipment maintenance problems can increase.
The real way to improve FCR is to work on waste. This tends not to have any unexpected consequences except a fatter wallet. Net time we look at the economics of FCR in a time of volatile feed and pig carcass values. How much FCR improvement is needed to justify those new feeders?