What is particle size?
Particle size refers to the particle size of the ingredients that make up the feed, i.e. the degree of grinding it has received before being offered to the animals. This parameter is commonly measured by the geometric mean diameter (GMD), which indicates the average particle size, and the standard deviation (SD) which reflects the variability in particle size within the mixture.
Although GMD and SD are influenced by the particle size of all the ingredients that make up the ration, most feed mills grind mainly plant-based ingredients, which in turn are the ones that are included in the highest proportion in the rations. Given their significant impact on both feed efficiency and diet cost, it is crucial these ingredients are optimally ground.
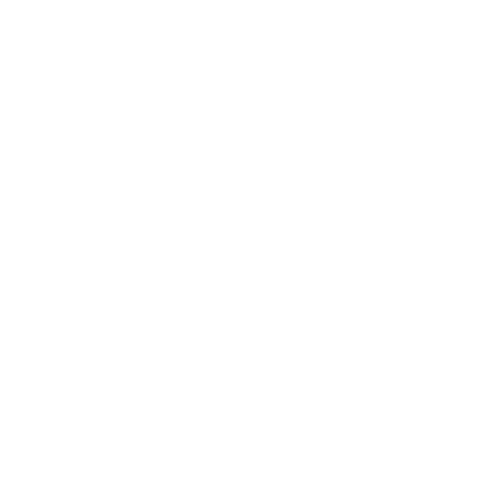
Why is particle size important?
Particle size plays a crucial role in feed digestibility. By reducing particle size, the contact surface is increased which facilitates the action of digestive enzymes and, consequently, improves digestibility and nutrient utilization.
During the 1990s, much research was conducted on the optimal particle size of cereal grains in swine diets, where its influence on nutrient digestibility was evidenced. Although particle size recommendations may vary according to the type of cereal, type of mill, and life stage of the animal, in general, particles in the 500 - 600 µm range were found to improve digestibility and the productive performance of pigs (Rojas et. al., 2017).
Table 1: Effects of corn particle size on apparent total tract digestibility (ATTD) of dry matter (DM) and gross energy (GE) and concentrations of digestible energy (DE), metabolizable energy (ME), and net energy (NE) of pigs.
Corn particle size μm |
P- value |
|||
---|---|---|---|---|
700 |
500 |
300 |
||
Consumption |
||||
Feed consumption, kg/day ![]() |
2.72 |
2.62 |
2.73 |
0.254 |
Consumption GE, Mcal/d |
10.66 |
10.15 |
10.69 |
0.628 |
Fecal excretion |
||||
Production of dry feces, kg/d |
0.27 |
0.23 |
0.23 |
0.001 |
GE in feces, kcal/kg |
4539 |
4568 |
4147 |
< 0.001 |
Fecal GE output, kcal/d |
1244 |
1032 |
962 |
< 0.001 |
ATTD of DM, % |
89.87 |
91.25 |
91.39 |
0.004 |
ATTD of GE, % |
88.26 |
89.7 |
90.89 |
< 0.001 |
Urine excretion |
||||
Urine production, kg/día |
6.11 |
5.9 |
6.81 |
0.001 |
GE in urine, kcal/kg |
33.23 |
33.01 |
29.19 |
0.049 |
Urine production GE, kcal/d |
206 |
197 |
194 |
0.075 |
Energy in diets, kcal/kg |
||||
DE |
3459 |
3477 |
3560 |
< 0.001 |
ME |
3385 |
3402 |
3488 |
< 0.001 |
NE |
2735 |
2739 |
2838 |
< 0.001 |
Energy utilization, % |
||||
ME:DE |
97.85 |
97.87 |
97.98 |
0.045 |
NE:ME |
80.79 |
80.5 |
81.35 |
0.165 |
Source: Adapted from Lee et. al. (2024).
In practice, however, it is common to find milling processes that are too coarse or uneven/non-uniform, with mills that lack adequate maintenance or do not have the productive capacity to handle the volumes required by the mill. When visiting farms, it is common to observe grain fragments in animal feces, indicating that the grain was not properly utilized and simply passed through undigested, representing a significant waste of nutrients and resources.
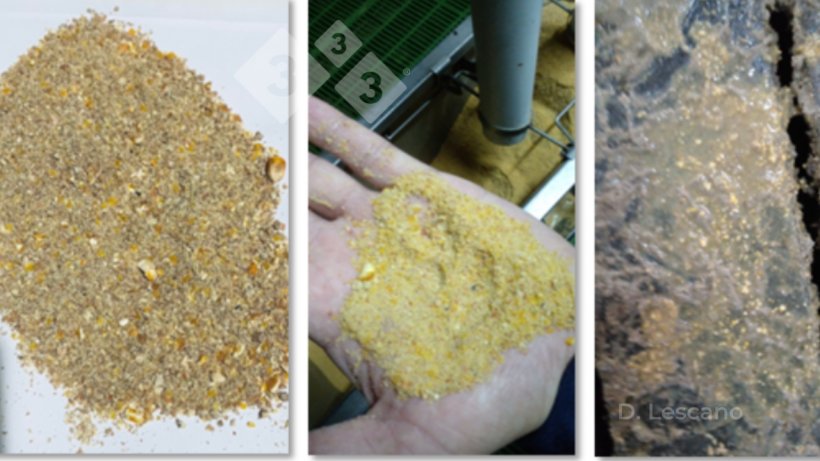
Figure 1. Irregular particle size in feed and feces. Photos provided by Diego Lescano.
Environmental sustainability in swine production has become a growing concern for governments and public opinion. In this context, feed particle size is presented as an accessible tool to reduce environmental impact. By optimizing particle size, the efficiency with which animals absorb nutrients is improved, which reduces the amount of waste generated on farms. This results in less excretion of undigested nutrients in the slurry, reducing both the volume of slurry and feed waste and minimizing gas emissions. This approach contributes directly to more efficient pig production with less environmental impact.
Kerr et al. (2020) conducted a study to compare the composition and gas generation of slurry from animals fed coarse and fine-ground feeds. The results indicated that the degree of feed grind impacts slurry composition and its volatile compounds, although no effects on greenhouse gases were observed. Thus, adjusting feed particle size could be an interesting measure to improve slurry quality and reduce gas emission losses, which is relevant for more sustainable farming practices.
Table 2. Slurry characteristics affected by particle size.
Particle size | NH4-N (μM g-1) | Sulphur (μM g-1) | pH | N (g L-1) | C (g L-1) | S (g L-1) |
---|---|---|---|---|---|---|
Coarse | 406 | 0.41 | 7.87 | 0.57 | 3.80 | 0.089 |
Fine | 358 | 0.37 | 8.05 | 0.48 | 2.88 | 0.085 |
P-value | .01 | .19 | .02 | .01 | .01 | .21 |
Source: Kerr et. al., 2020.
Table 3. Main volatile compounds in slurry as affected by particle size.
Particle size | Acetic (mmol g-1) | Propionic (mmol g-1) | Butyric (mmol g-1) | Total* (mmol g-1) | Phenols (μmol g-1) |
---|---|---|---|---|---|
Coarse | 188.0 | 22.0 | 16.0 | 237.0 | 1.5 |
Fine | 128.0 | 13.0 | 8.0 | 156.0 | 1.3 |
P-value | .01 | .01 | .01 | .01 | .01 |
Source: Kerr et. al., 2020. *Total volatile fatty acids (acetate, propionate, butarate, isobutyrate, isovalerate, valerate, isocaproic, caproic, and heptanoic), phenols (phenol, cresol, ethylphenol, and propylphenol).
We can't talk about environmental sustainability without also considering the economic sustainability of farms. Nutrition represents approximately 70-80% of the cost of pig production. If a portion of feed is lost in the pits of the farm due to poor grinding, the economic impact can be considerable.
Lescano et al. (2017) observed that each 100 µm increase in particle size results in a 2.72% increase in the feed conversion ratio (FCR) for animals with a sale weight greater than 125 kg. Similarly, Wondra et al. (1995) showed that the FCR increases 1-1.5% with each 100 µm increase in particle size, considering animals with a sale weight close to 105-110 kg.
According to recent data from trials conducted by Diego Lescano in Argentina (2023), the correlation between geometric mean diameter (GMD) and the percentage of particles larger than 1000 µm in ground corn samples, using corn and soybean meal based diets, was evaluated. The impact of these factors on production performance, as measured by the feed conversion ratio (FCR), and on the economic benefit to the animals was examined.
The conclusions indicate that every 1% increase in particles larger than 1000 µm results in an 8 µm increase in GMD, leading to a 0.20% increase in FCR. This reflects a reduction in feed efficiency. These results underscore the need to control particle size to improve the feed conversion ratio and reduce costs associated with improper grinding.
Conclusion
Feed particle size is not only a tool for improving feed efficiency but is also a key factor in reducing the environmental impact and economic sustainability of pig production.
Practical recommendations
Continuous monitoring of particle size at a set frequency, as well as constant maintenance of the mill to avoid breakage and wear that can result in increased particle size.