A common limit to pig performance as sale weights increase is feeder access. Producers and equipment suppliers often size feeders based on the number of ‘holes’ the feeder offers without regard to the issues surrounding the ‘quality’ of the eating space or ‘hole’.
Gonyou and Lou (1997) using pigs with weights up to 95 kg (209 lb) concluded that the best compromise for feeder depth (distance from the front lip of the feeder pan to the feed delivery point) for grow-finish pigs was 20-30 cm (8.9 in to 13.3 in). They concluded that the ideal feeder depth for 95 kg (209 lb) pigs was 32 cm (12.6 in). This suggests that a majority of the feeders installed in production facilities in the US and Canada today which have depths of 20-25 cm (8-10 in) are limiting to pig performance as sale weights increase.
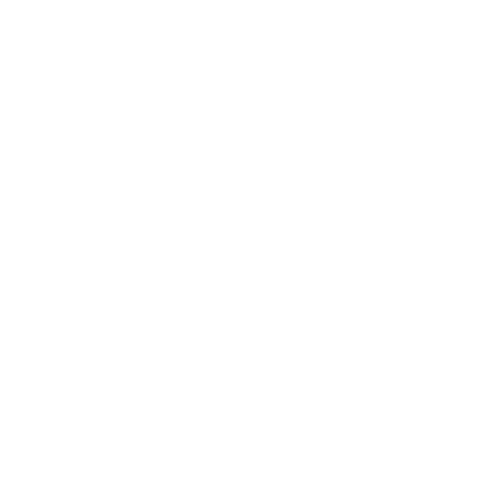
The problem with increasing feeder depth is smaller pigs at time of placement stepping into the feeder to access feed and then tracking feed out of the feed pan. However this has not been an issue with ‘wean-finish’ feeders where pigs are grown from 5.5 kg (12 lb) to slaughter weight on the same feeder. In this author’s experience, as sale weights increase, feeders must have at least 25.4 cm (10 in) of depth from the front lip to the feed delivery device or agitator plate with 28-30.5 cm (11-12 in) preferred for dry feeders. If the distance is less than this, pigs end up pushing against the feeder with the crown of their forehead and/or have difficulty accessing the feed agitator plate.
The width of the feeding space is defined by the shoulder width of the pig. Petherick (1983) defined shoulder width in relation to pig body weight as:
Width (mm) = 64.0 x (bodyweight, kg)0.33
Width (inches) = 1.942 x (bodyweight, lb)0.33
To allow for pig movement at the feeder, feeder spaces should be sized based on 1.1 times the shoulder width. Table 1 lists the estimated shoulder width in relation to pig weight and the estimated width of feeder spaces based on these shoulder width dimensions. This table supports the recommendation that feeders for today’s production facilities should have a minimum feeder ‘hole’ width of 3.5 cm (14 in).
Table 1. Shoulder width of growing pigs in relation to pig weight and estimated feeder ‘hole’ widths necessary to accommodate this dimension. Based on Petherick (1983).
Pig Wt | Shoulder Width | 1.1 x Shoulder Width | |||
kg | lb | cm | in | cm | in |
18.2 | 40 | 16.8 | 6.6 | 18.3 | 7.2 |
27.3 | 60 | 19.1 | 7.5 | 21.1 | 8.3 |
90.9 | 200 | 28.4 | 11.2 | 31.2 | 12.3 |
100.0 | 220 | 29.2 | 11.5 | 32.3 | 12.7 |
109.1 | 240 | 30.2 | 11.9 | 33.0 | 13.0 |
118.2 | 260 | 31.0 | 12.2 | 34.0 | 13.4 |
127.3 | 280 | 31.8 | 12.5 | 34.8 | 13.7 |
136.4 | 300 | 32.5 | 12.8 | 35.6 | 14.0 |
145.5 | 320 | 33.0 | 13.0 | 36.3 | 14.3 |
The table also highlights a common feeder problem with swine nursery units. Many nurseries now house pigs until 25 kg (55 lb) or heavier. The vast majority of feeders sold in the US for placement in swine nurseries still have feeder ‘holes’ that are 15.25 x 15.25 cm (6 x 6 in). Based on shoulder dimensions these feeders most likely limit feed intake or at the minimum limit pig access to feed by limiting the number of usable spaces that pigs can eat from unless the spaces/holes are 20.3 cm (8 in) wide.
Figure 1. Twelve ‘hole’ 2.13 m (84 in) long double-sided feeder with marked pig (almost 136 kg (300 lb)) destined for removal and sale immediately after the picture was taken.
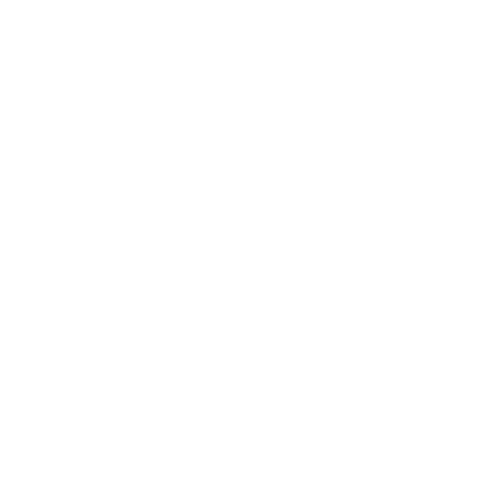
Figure 2. Ten ‘hole’ 1.83 m (60 in) long double-sided feeder 2-3 weeks prior to first pig removal for sale.
Similar sizing issues arise when drinking water is furnished in trough or cup/bowl drinkers. Pigs grow in 3 dimensions (length, width, and height) so the need to account for increases in head dimensions for these devices as slaughter weights increase is also a reality.
Because of both genetic and nutritional improvements, rates of lean deposition have increased since the move to confinement production began in the 1970’s. As a result, the heat production by the growing pig has increased. The best estimate is that metabolic heat production increases 12-15% every 10 years (Figure 3). While previous data sets on heat production by growing pigs stop at 100 kg (220 lb) (Brown-Brandl et al, 2004), more recent data (Brown-Brandl et al, 2014) not only supports the continued increase in total heat production over successive generations (16% increase since ASHRAE (2001)) but also documents heat production for growing-finishing pigs up to 130 kg (286 lb).
Figure 3. Heat production by growing pigs based on Brown-Brandl et al (2004).
This suggests that managing the pig’s environment with the goal of heat removal is an increasing need, especially when pens are more crowded due to heavier sale weights and the pigs can’t modify their posture in the pen as readily to dissipate this increase in metabolic heat. Nienaber et al (1997) have suggested that the upper critical temperature threshold declines rapidly when pigs weigh more than 75 kg (165 lb). They further suggest that pigs with high rates of lean gain (such as today’s genetics) are much more sensitive to high temperatures than pigs with medium rates of lean gain. This conclusion was supported by the results of Renaudeau et al (2011).