On several fronts, emphasis is increasingly being placed on reducing emissions of polluting gases, and swine production is not exempt. In addition to complying with current regulations, new factors come into play such as the high prices of inorganic fertilizers and energy, which means that treating slurry is seen as a valuable asset rather than a problem to be managed, both in terms of its use as a fertilizer and in terms of energy production.
In this particular case, we are going to focus on the use of slurry as an energy source at the farm level, which is one of the strategic projects of Agrocat, an agricultural cooperative. The system is already being tested on one of its farms, located in Catalonia, Spain, with 800 sows producing 20 kilo pigs. We visited the farm and were accompanied by agricultural technical engineer Rubèn Masnou who is in charge of the cooperative's agro-chemical and environment department, and Carles Mas, who is in charge of the farm.
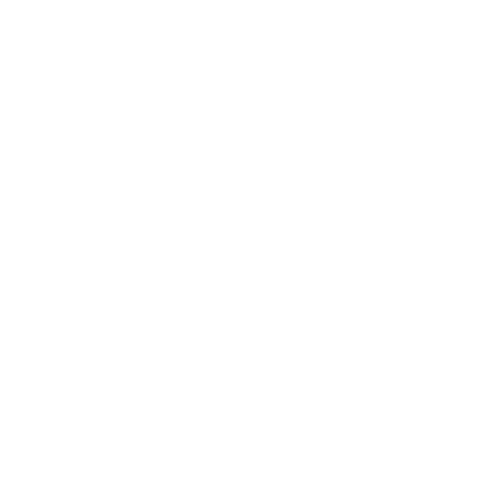
To comply with the emission reduction level, it was decided to cover the slurry storage pit, thus minimizing the emission of ammonia into the atmosphere. This covering creates an anaerobic environment which, in addition to obtaining a digestate with greater fertilizing power and that is more homogeneous than fresh slurry with fewer odor problems, also generates biogas (with a CH4 concentration of over 64%), which was decided to be used as a source of self-sufficient energy for the farm.
Installation and operation
The slurry pits under the buildings are emptied weekly and the fresh slurry is channeled by gravity through a pipe to the receiving tank, from which the slurry is pumped daily at a rate of about 10m3/day to an adjacent 22x11x4 m concrete tank covered by an EPDM propylene tarp, supported by an internal structure, where it undergoes anaerobic digestion. The final digestate is stored in an adjacent, uncovered structure.
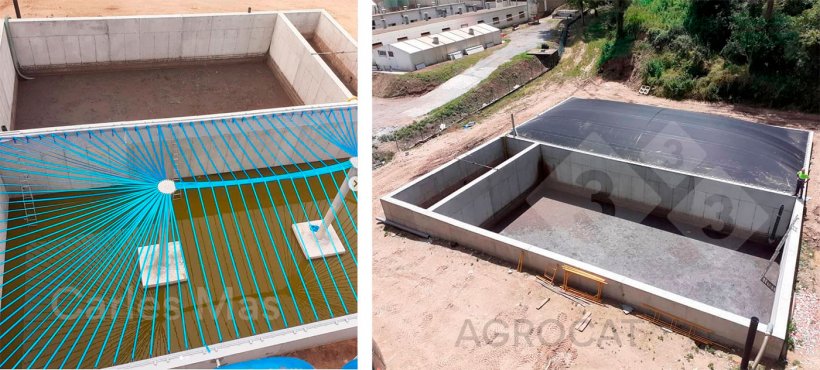
Photo 1: Aerial view of the existing rope structure under the propylene tarp. Photo 2: Aerial view of the biogas plant which consists of a reception area for fresh slurry, anaerobic digestion area, and digestate storage area.
In this case, co-digestion is not carried out and no agitator is available for the time being. Biogas production varies throughout the year depending on the enviromental temperature and slurry composition.
The biogas produced is retained under the propylene tarp and is channeled to the farm. Biogas production, from slurry alone, is low but sufficient to be used to heat the nursery barns almost all year round. On days when there is insufficient biogas production, the nurseries are heated with the farm's existing biomass boiler.
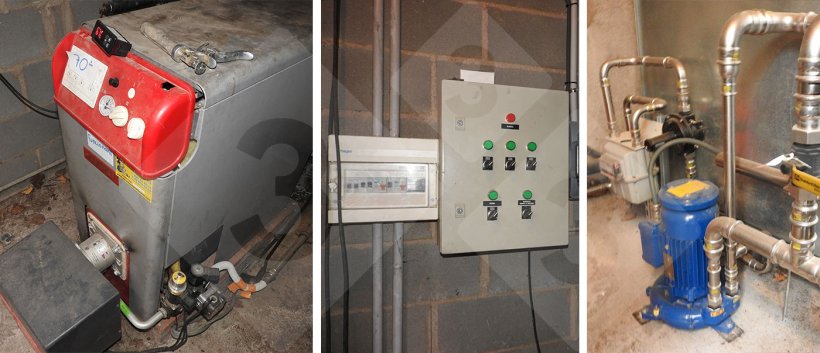
All biogas production is associated with the production of hydrogen sulfide, which is why the pipe that channels the gas slopes towards a catch basin to collect part of this hydrogen sulfide contained in the gas condensation so that it can be redirected to the digester. Since the H2S levels detected are very high (2500 - 3500 ppm), they oxygenate for about one hour per day to lower the concentration.
The digestate obtained is a more homogeneous fertilizer than fresh slurry and, as we have already mentioned, it has greater fertilizing power since it contains a greater amount of ammoniacal N, which is easily assimilated by the plants. Taking into account that this digestate can also release a certain amount of ammonia into the atmosphere, the way to minimize this is being studied (burial or acidification).
Economic value
Initially, high investments are associated with this type of solution, but if we take into account that we may have to cover our lagoons or slurry reservoirs to comply with legislation requesting a reduction of ammonia emissions , and that we will create an energy resource to be used on our own farm (circular economy)- in the actual context of the high prices of energy and fertilizers- .this investment can have an attractive return on investment.
The basic investment has been estimated at €49,000 without taking into account the construction of the concrete tanks, to which some components such as an agitator, a carbon filter for the hydrogen sulfide, and some gas measurement and control equipment would have to be added.
In this first year of operation and testing, the plant has produced about 5,500 m3 of biogas and expects to reach a production of 12,000 m3, enough to offset the investment of the covering and installation in 5-6 years.
At current energy prices, this represents a savings of approximately €10,000/year, in addition to reducing ammonia emissions by almost 100% and obtaining a better organic fertilizer.
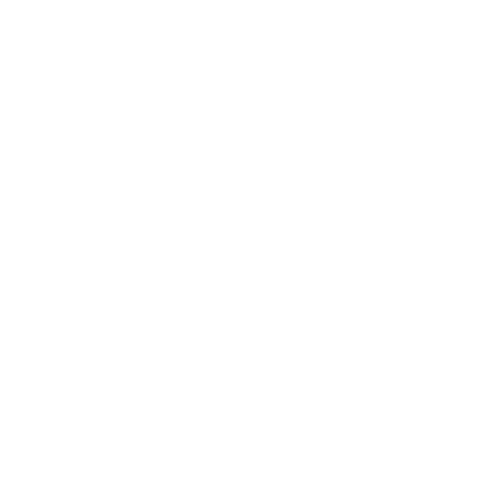
333 Staff