We visited the Coagra farm, which is located in the Spanish province of Lleida and is owned by Jaume Alòs. The farm has a number of characteristics that make it uncommon within the context of the Spanish sector. Jaume Alòs is an independent farmer and that makes him value the implications of his decisions in the whole chain: investment, costs, and the price paid to the farmer. Another very evident factor is the good work done by his wife Nuria regarding the analysis and financial control of his project. And the third element stems from its status as a family farm, where we can see the pride in the inheritance received and the excitement generated within the family by the possibility of handing down the farm to the next generation with his daughter Abril being interested. In order to improve the balance between work on the farm and family life and to improve the future of the project, the farm expanded a few years ago to be able to hire personnel and it also incorporated technology.
The system consists of a farm of 400 sows, organized in three-week batch farrowing and weaning at 26 days. One-hundred percent of the production is finished in different external finishing units. The sow farm works with a dynamic group with electronic sow feeders with a built-in scale to adjust the ration to the current weight of the animal. They also have electronic feeding in the farrowing house. They work with Danish genetics for the sows and use a halothane negative Pietrain as a terminal sire.
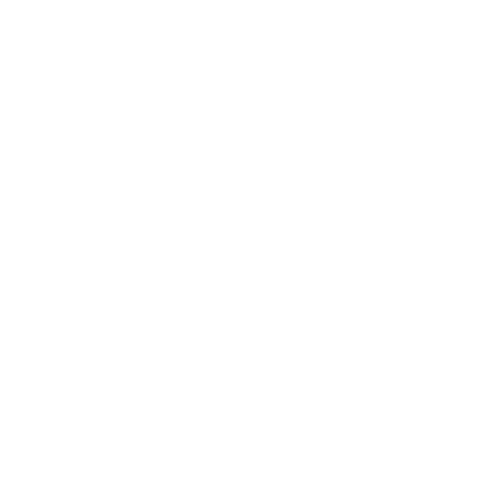
The objective of the visit was to review a finishing pig barn in large groups using automatic weighing and automatic sorting of the animals.
It is a newly built barn that completes the need for finishing places in order to be able to finish out the entire production. The previous experience with automatic feeders and scales in the sow unit was a determining factor when deciding on this technology for the finishing unit. The barn is divided into two large pens (male and female) that occupy 100% of the barn space (Figure 1).
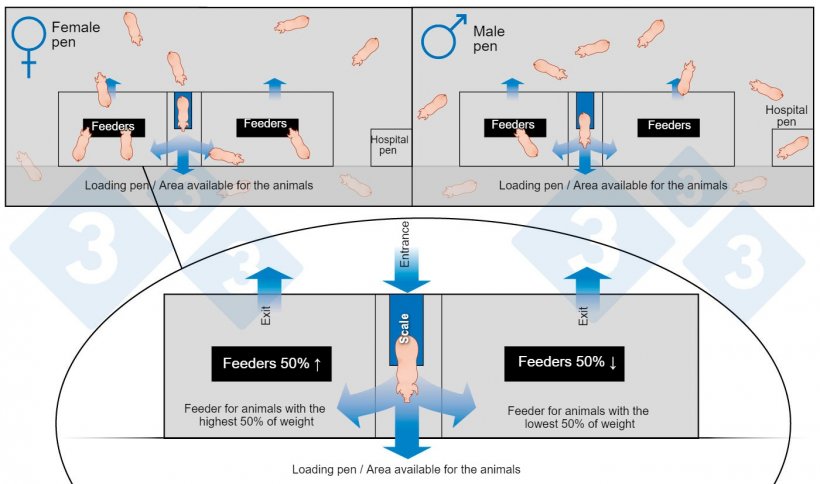
Figure 1: Diagram of the finishing barn with large groups and automatic sorting.
The area designated for preparing the load for slaughter is set up with panels when necessary. The rest of the time it is kept as an area available for the animals. There are two 3.5 x 3.5 m hospital pens.
Basic operation:
This system works without RFID tags. Using a door system, similar to what you would see in an electronic sow feeder, the animals enter a scale. Based on weight, the system separates the top 50% of weights and the bottom 50% of weights and each group is directed to an indoor pen located to the right and left of the scale (Figure 2). Each feeding pen has four double hoppers with three head spaces. Once the pigs finish eating, they return to the main group through a single exit door. The finishing unit has two silos so that each group can receive the most appropriate feed for its weight. Every silo has a weighing system.
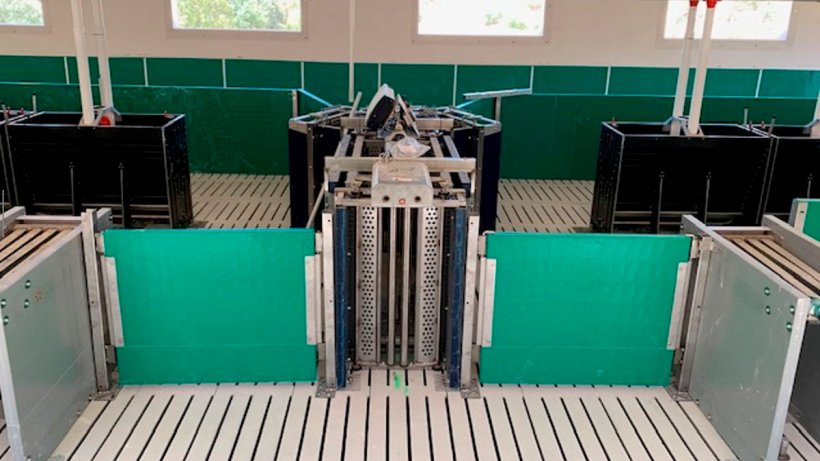
Figure 2. The system separates the top 50% of weights and the bottom 50% of weights and each group is directed to an inner pen located to the right and left of the scale.
Since the pigs' current weights are available, the loading schedule can be programmed precisely several weeks in advance. When a load is to be prepared for slaughter, usually the day before, the system is told how many animals and from what weight they are to be separated. The system must be activated manually to ensure that the pen to where the batch going to slaughter will be diverted has been set up correctly. When passing through the scale, animals weighing more than the set weight are diverted to the loading pen until the established quota is reached. This pen is equipped with drinkers so that the group can be fasted properly without interfering with the consumption of the rest of the animals.
Facilities:
The barn we visited is a new construction. Regarding construction costs, there is clearly an initial investment in the scales and the system for sorting the animals, but this type of design represents a considerable saving in feeders, drinkers, panels, and gates. Jaume is also a strong advocate of installing automatic weighing systems for the silos. This tool allows him to better schedule feed deliveries, avoid feed shortages and also monitor if there is any incidence of reduced consumption that could be an early warning of a health problem.
Space:
The absence of aisles, fewer feeders, etc. in this type of finishing system allows for greater capacity. Specifically, in this barn they went from 820 places in a traditional finishing system to 1000 places under the large group system, meaning 20% more places. The finisher barn keeps a single origin and only receives animals from the farrowing batch of the sow farm. The animals are usually at a density of 0.75 m2/pig and never below 0.70 m2. Sometimes trying to optimize the use of this space by bringing in animals from a second origin can cause more losses due to sanitary problems.
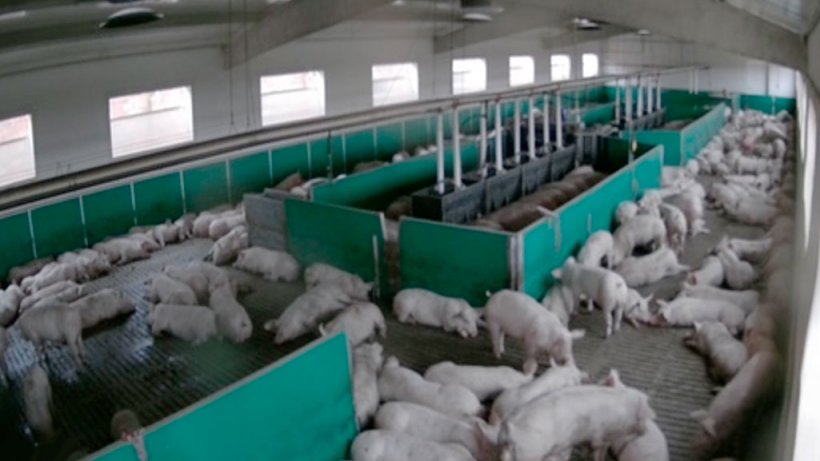
Figure 3: Finishing barn using 100% of the space, including the load preparation area.

Figure 4: Finishing barn with the load preparation area set up.
Mortality and incidence of vices: After almost three batches, no differences in mortality have been observed. The owner's observations are that the incidence of vices and fighting is lower in this type of design. The animals have more space to flee, hide, and mix with others, and also the design of the facilities allows for some optical barriers.
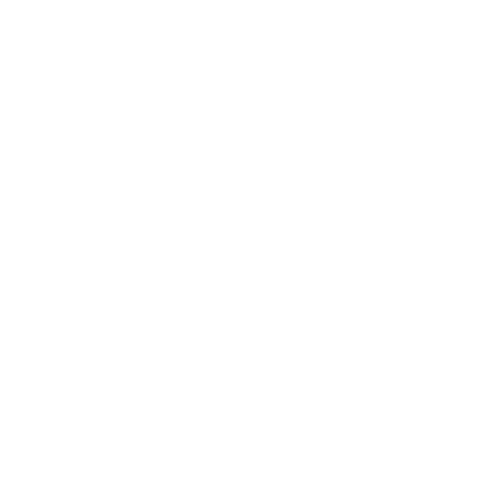
Better climatic comfort: The finishing barn has cameras for remote monitoring. One of the observations made by Jaume is how the animals vary their resting areas depending on the weather conditions. Having much more surface area gives them more possibilities to choose or avoid areas where they detect drafts or hotter areas, an option that is much more limited in a small pen system.
How much does the large group system contribute to the farm's day-to-day operations and operating costs?
Jaume Alòs is a strong believer that technology helps us to do our work better, but human labor is still irreplaceable. The silo weighing system and access to the scale allows us to know if the group of animals is following their usual feeding pattern, which gives us an early warning system, should disease appear (Figure 5). It monitors how much feed the pigs have consumed and how many visits to the feeding trough have occurred.
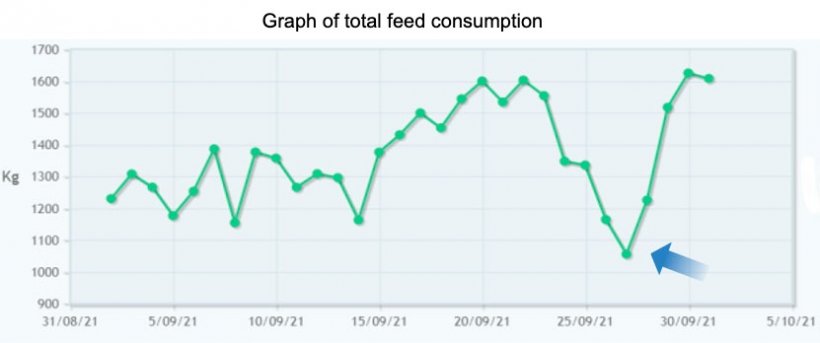
Figure 5: Decrease in consumption observed on the farm before the appearance of symptoms of respiratory problems. Early detection of the problem allowed for a better treatment outcome.
There is no identification of individual animal consumption and the system does not replace supervision by personnel, which in this case is done twice daily.
This farm works with two silos and 4 different feeds:
- From entry at 18-20 kg until 25 kg
- From 25 to 40 kg
- From 40 to 70 kg
- From 70 kg until exit
With the combined information on the actual amount of feed in the silos with the actual weight of the animals, diet changes are optimally performed. Being able to better adjust feed changes to the actual weight of the animals brings an improvement in the cost of production compared to the standard finishing system in which the feed change occurs for the whole group at the same time and without having the actual weights of 100% of the animals. Although there is no difference in the feed conversion rate, the cost of production is improved, with a higher average daily gain in this system.
What does this system contribute in terms of delivery to the slaughterhouse?
The process of preparing the loads is much faster, more accurate, efficient, and less stressful for animals and personnel. After almost three batches, the payment received for the animals from this system shows an advantage of about 1.5 € cents/kg live weight over animals of the same origin, same genetics and nutrition from finishing barns with 3 x 3 m. pens. Basically, the percentage of animals delivered within the slaughterhouse specifications is above 95%. Having accurate data on the weight of the animals that make up the delivered batch also allows sharing this information with the slaughterhouse in case there is any incidence with respect to the weights at delivery.
Washing and preparing the barn is also significantly faster and easier as there are fewer sides, corners, hoppers, etc.
This farm is an example of what precision livestock farming can bring to finishing.
We would like to thank the Alòs family for their time, kindness and for all the information they gave us. Jaume's eagerness to try new things, Nuria's good analysis, together with the anticipation of this new generation in Abril make for a winning combination.
333 Staff