Protocols to prevent the transmission of infectious disease between swine production facilities on fomites (i.e. inanimate objects) are a critical aspect of every biosecurity program. Regardless of whether your farm is an independent operation or part of a large system, investing in professional tools can eliminate the need for service personnel to move the same tools between premises.
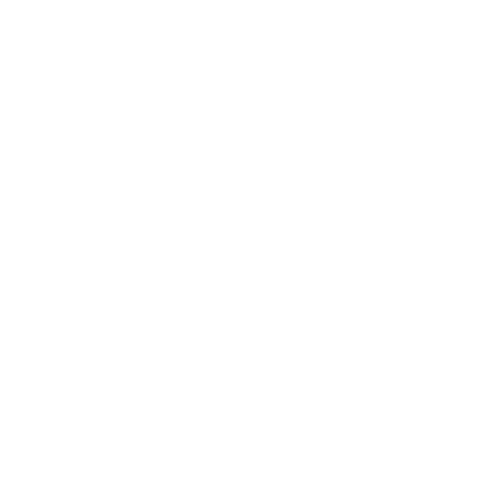
Applying the Tip
In today’s swine industry, production facilities are often multi-million dollar investments. Depending upon prevailing market conditions and the size of the operation, annual sales can easily reach into the multi-million dollar range. As a result, pork producers are able to justify the costs associated with large annual biosecurity and health management programs that can prevent the financial losses associated with disease outbreaks.
In regions that have a high density of pork producers, it is common for professional service organizations (e.g. electricians, ventilation specialists, and plumbers) to specialize in servicing animal agricultural operations. These organizations have developed an appreciation for biosecurity requirements and commonly work together with producers to implement their biosecurity priorities (e.g. personnel downtimes). Large production systems with their own facility operations departments commonly train their service personnel in best practices of biosecurity.
Service personnel, such as electricians and plumbers, are accustomed to owning their own tools and to moving these tools from assignment to assignment. When we consider the potential for the transmission of disease from one swine facility to another, this type of practice is of critical concern. Managing the risks associated withevery potential disease transmission pathway has become even more important with the Porcine Epidemic Diarrhea virus epidemic across Asia and the Americas. A unique characteristic of PEDv appears to be the very low minimum number of virus particles required to cause disease. As a result, minor deficiencies in the effectiveness of biosecurity program have the potential for allowing significant financial losses.
Even though many professional service providers are accustomed to meeting minimum standards like those outlined in Table 1, it is relatively easy to argue that many of these tools are difficult to clean and, in many cases, they may be damaged by water, soap, and disinfectants.
Table 1
Verify acceptable downtime and biosecure management of personnel, vehicle, and tools between premises |
Outline the location and usage of the tools at the previous location |
Disinfect outside surfaces of tool carrying cases upon entry to the facility |
Disinfect individual tools prior to use within each facility |
In one large production system in western Canada, farm owners recognized that the cost of purchasing specialized tools for each production facility represented a relatively small investment in relation to the potential financial losses due to disease. They asked their service providers (i.e. electricians, plumbers, etc) to create a minimum list of tools needed to complete their service related work. These tools were purchased and stored within the production facility under environmental conditions that were not detrimental to the tools. As well, the tools were dedicated to the use of the service provider and, although the production facility owned the tools, the service provider was responsible for their proper maintenance and storage.