Lately, climate changes have forced governments around the world to enforce legislation to reduce the carbon footprint from all parts of society including pig production. Many new technologies supporting these demands have evolved.
Green-house gases
Green-house gases (GHG) have become of increasing concern during the last decades because of their potential harmful effects on the global climate. Emission of gases from livestock production, that includes carbon dioxide (CO2), methane (CH4) and nitrous oxides (N2O or N2X), is one of the major contributors of GHG. In addition, ammonia (NH3) emission is also of concern with respect to sensitive nature.
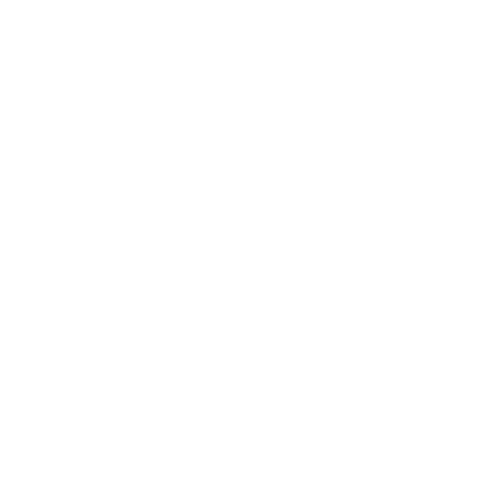
In pig production, manure management is a source of both CH4 and N2O emissions. Liquid manure systems dominate while dry manure and straw-based systems are more present in extensive and organic pig production. Most GHG emissions from liquid manure management are in the form of CH4 while N2O is less present and develops more in dry manure systems. Here, the focus is on large scale pig production and therefore mainly on liquid manure systems.
Table 1. Distribution of CO2-equivalents (CO2-e) emission per pig from birth to finish at 115 kg (SEGES, 2021).
Kg CO2-e | Distribution % | ||||
---|---|---|---|---|---|
Piglet* | Wean-30 kg | 30-115 kg | Total | ||
Feed intake | 26 | 40 | 119 | 185 | 67 |
Methane, feces | 6 | 6 | 35 | 47 | 17 |
Methane, intestinal gases | 2 | 2 | 11 | 15 | 6 |
N2O, feces | 3 | 2 | 12 | 17 | 6 |
Energy use | 3 | 4 | 5 | 12 | 5 |
Total | 40 | 54 | 182 | 276 | 100 |
*Including contribution from the sow.
While attempting to reduce GHG it is important to know how it is possible to obtain the highest reduction with the least cost. From the table above it is clear that feed constitutes the largest contributor to GHG while methane in feces is second largest. Obviously, the feed contribution can only be reduced by higher feed efficiency which is mainly attributed better genetics. So, therefore focus is mainly on reduction of methane, N2O and more energy conserving technologies. The most important technologies are presented below.
Slurry cooling
The temperature of slurry is usually around 20-24 oC, similar to the room temperature in the pig unit. At decreasing temperatures, the growth of microorganisms will be lower and the production of CH4, CO2 and NH3 will decrease exponentially with decreasing temperature.
Table 2. Advantages and disadvantages of slurry cooling.
Advantages |
---|
|
|
|
Disadvantages |
|
Slurry cooling is established by installing 25-30 mm PEL-pipes in the concrete base of the slurry pit. The pipes are installed with a distance of 30-40 cm and attached to the reinforcement steel. A closed circuit of pipes connected to one or several heat pumps carries cold water through the base of the slurry pit reducing the slurry temperature while heating the water inside the pipe. The heat pump works like a refrigerator and cools the water while transferring the recovered heat to a pipe system for hot water used for heating areas where the heat is needed typically farrowing and weaner units. The heat pump is operated by electricity and the output of heat is generally 4 times higher than the input of energy in kW. If the recovered heat is utilized fully then the GHG effect is 1.0, 0.8, and 3.4 kg CO2-e per pig including sows for piglets, 7-30 kg pigs, and 30-115 kg pigs, respectively with a cooling effect of 10 W/m2.
Table 3. Slurry cooling – effects and investment cost.
Slurry cooling – cooling and emissions | ||||
---|---|---|---|---|
Cooling, W/m2 | Reduction of emission, % | Investment, EUR/pig place | ||
NH3 | CH4 | Odour | ||
10 | 8-14 | 10-15 | 8 | 7-10 |
20 | 15-25 | 20-25 | 15 | 10-13 |
30 | 22-32 | 30-35 | 20 | 11-14 |
Frequent removal of slurry
Slurry is a mixture of urine, feces, and water, and when left unmanaged it can decompose and produce CH4. By removing the slurry frequently and applying it to crops as a fertilizer, the decomposition process can be controlled. The frequency of slurry removal is generally once every 7 days.
Table 4. Advantages and disadvantages of frequent removal of slurry.
Advantages |
---|
|
|
|
|
Disadvantages |
|
In conventional slurry systems plugs are pulled via a rod through the slot opening. It is important to start with the slurry plug in the section furthest away from the reception tank to remove all waste. The slurry is transferred in a pipe from the pig section to the main pipe which leads the slurry into the reception tank. The system might be automated including valves placed strategically in the pipeline which are opened via an electrically switch.
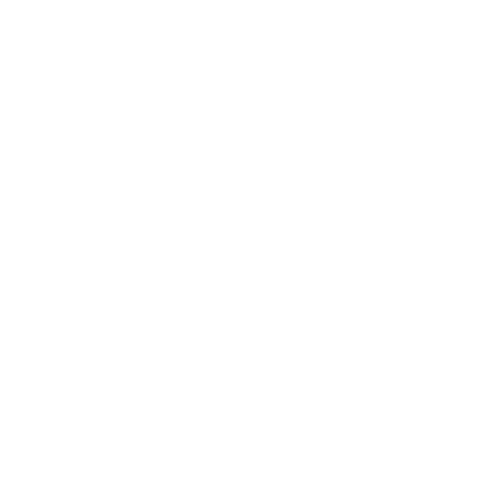
Table 5. Frequent removal of slurry – effects on emission.
Weekly removal of slurry, reduction of emission, % | ||
---|---|---|
NH3 | CH4 | Odour |
0 | 90 | 20 |
Acidification
An acid is added and mixed with the slurry to reduce its pH level.
Advantages |
---|
|
|
|
|
Disadvantages |
|
|
The technology comprises a conventional slurry system inside the pig barns but without plugs. The slurry is released from the barns daily and stored in a process tank. Then an acid, commonly sulfuric acid (93-96% concentration), is carefully added to the slurry. Acid is added from a container placed on weigh cells to control the consumption. Around 11-13 kg of acid is used per ton of slurry. Sensors measuring pH constitute the main basis of control. When the pH level in the slurry-acid mix reaches 5.5 most of the mixture is pumped back into the pits of the pig barns while the rest is pumped to a storage tank. The pit area of the pig barns is divided in units of 1,000-1,500 m2 which is emptied and filled with processed slurry.
Odour emissions might be reduced by adding a drum filter which separates the solids from the liquid. The combined system is certified as BAT and might reduce odour by 61%.
A recent study at Aarhus university indicates that it might be possible to reduce the amount of acid to 2-3 kg/ton of slurry while obtaining a strong effect on CH4 and NH3 reduction. Therefore, low-dose acidification might be a viable strategy for GHG mitigation. Furthermore, new investigations using acetic acid (CH3COOH) instead of sulfuric acid might reduce cost of operation and make the system more applicable in countries where sulfuric acid is not readily available. Moreover, the hazards of using a weaker compound like acetic acid are less.
Table 6. Slurry acidification – effect on emission.
Slurry acidification, reduction of emission, % | ||
---|---|---|
NH3 | CH4 | Odour* |
65 | 40-65 | 61 |
*Reduction if combined with drum filter.