Pig feeds typically require 15 to 25 percent crude protein to provide the limiting amino acid intake needed for growing pigs. Alternatives to traditional sources of protein in feed such as soyabean and fishmeal include cottonseed, perilla, flax and sunflower. Alternative feed protein sources derived from processed animal or insect materials have also been investigated. The commercial value or uptake of these alternative sources on any major scale requires careful examination of their business model, price structure and safety. Major companies now offer insect larvae-based protein products intended for inclusion in pig feed. The larvae of the black soldier fly (BSF) is an impressive consumer of vegetable/animal waste materials, converting 12 to 25 % of solid biomass into larvae then capable of harvest for feed protein materials. So, for these several companies developing insect larvae protein sources deliverable to feed mills and farmers, the larval yields, safe sources of larval substrate, safety testing of products, comparative costs of production, etc. all impact its sustainability.
Regulatory framework
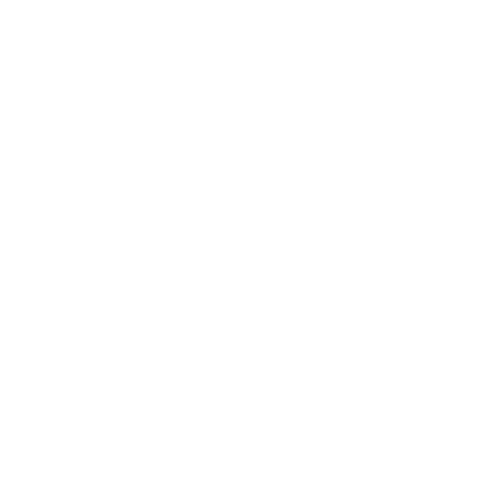
Many government guidelines restrict the sale of products containing insect source materials and sources of waste substrate on which larvae products can be grown and marketed, with a rigorous HACCP (Hazard Analysis and Critical Control Point) safety guideline plan needed to market BSF larvae as an animal feed ingredient. For pig feeds, it is important to restrict access of any larvae to sources of waste containing either ruminant or pig (intra-species) materials.
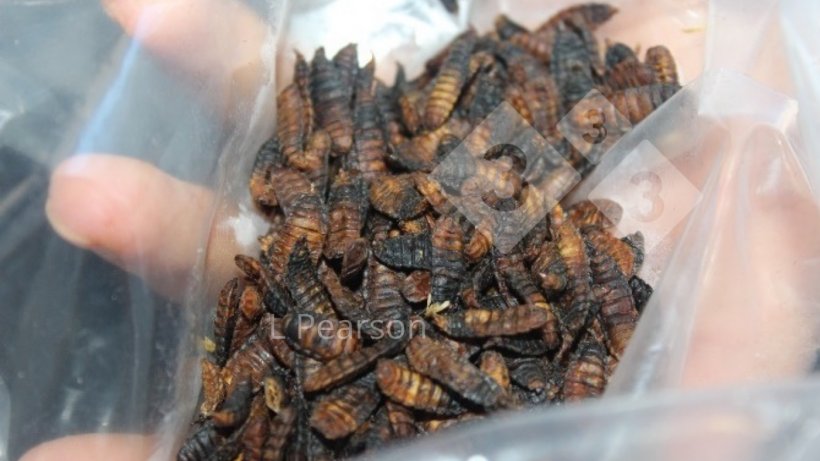
Business framework
Commercial production of insect larvae intended for animal feed requires suitable sources of insect substrate (eg cheap waste materials), HACCP controlled insect rearing and processing processes, product and process testing for known pathogens and heavy metal content. The growing period of larval production in shallow bins at commercial scale often requires high labour inputs. The storage and use-by dates of products requires determination. The current cost comparison of insect larvae to all other feed protein sources remains unfavorable. The actual conversion rate of BSF larvae turning substrate materials into usable protein product requires close scrutiny – assuming an 80 percent water content of waste material substrate then 1 metric tonne of waste delivered to a commercial facility would still only produce 50 kg of dry weight larvae.
Safety issues
- Pathogens: The substrate used for insect larvae production (eg vegetable and animal waste materials) can be complex and contain various bacterial, fungal and virus pathogens. BSF larvae can retain numerous known hazardous bacteria, eg Salmonella over the production period in their gut and integument. Successful processing aimed at eliminating these pathogens therefore needs to carefully exclude production materials or personnel. Elimination of the risk of prion material occurring in larval products can only be achieved by complete restriction of ruminant or pig (intra-species) materials. Hardy pathogenic fungi and parasites such as Enterocytozoon and Cryptosporidium and nematodes can be a significant risk in their ability to persist in insect larvae materials. It is possible that genetic transfer of unfavorable plasmids such as antibiotic resistance genes may be facilitated by feeding insect larvae to animals. Recent history has demonstrated the ability of pig feed materials contaminated with viruses to travel across the globe, with devastating consequences for pigs.
- Heavy metals and pesticides: Insect larvae are tough customers and are known to accumulate heavy metals such as cadmium, lead, mercury and arsenic, so batch testing is necessary under a HACCP. Other more beneficial studies have shown that BSF larvae can break down antibiotics and pesticides.
What about turning manure waste and waste human food (swill) into animal feed protein?
It is possible if animal manure (e.g. chicken) and waste foods are carefully sourced, processed and tested then used as substrate for BSF larvae, then processed BSF larvae could then be fed as a feed ingredient to other species, eg pigs or aqua. But given the vast number of pathogens which realistically cannot all be analyzed, unpredictability, variability of manures/food-scraps, potential risk and perception it is doubtful this concept will meet regulatory approval in many countries. Although manure can be sourced locally to reduce the spread of exotic diseases, and processing steps can eliminate pathogens, passive transfer of diseases by insects are still a major concern. If BSF larvae are fed something which can be classified as waste human food (swill), unless an approved process occurs, then the larvae will also be classified as swill.
Realities of insect larvae farming: Some pros and cons
Pros | Cons |
---|---|
Improved feed production sustainability and circular principles | Commercial insect farming requires new skills and complexity |
Insect larvae have high conversion efficiency | Unknown hazards and risks |
Less reliance on transport and importation of feed ingredients | Cost of production of usable feed ingredient is much higher (2-3 X) compared to current market leaders eg soyabean meal |
Requires less land and water input compared to other feed protein sources | Hygiene risks are more complex and costly to monitor |
High cost of production can be overcome with further investment and scale | More plentiful substrates eg manure waste have no regulatory approval and are hard to transport |
Creates innovation and knowledge which can be used to improve future animal feed resilience | Commercial scale insect production may require higher capital and labour costs |