In any sow farm, the design of the farrowing house is an essential subject for its economic and productive success.
The design includes many factors, such as the number of farrowing pens, size of the rooms, size of the farrowing pens, crates, heating, ventilation, etc.
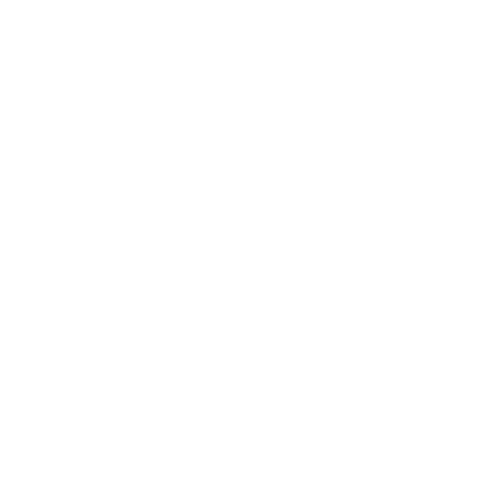
Our aim in this and the following article —which will be published over the next few months—,is to answer most of these questions. To achieve so, we have worked closely with two very well known experts, Heraclio Corchón and Javier Lorente, both of whom have extensive experience in farm management and in design and construction of farms.
Number of farrowing pens
Nowadays this is one of the first questions that arises when starting a new project. Hyperprolificacy forces the farmer to provide a greater number of pens, which increases investment significantly.
Lorente is clear: “around 10% over your weekly objective. If your objective is 50 farrowings per week: 55-56 farrowing crates per week. With hyperprolific females, extra room is needed for nurse sows.”
What room size would you go for ?
How are we going to distribute the farrowing rooms: rooms for weekly batches, bigger rooms, smaller one?
Lorente is not in favour of small rooms. He believes a good option would be to have rooms that allow splitting the weekly batch in two. “If my weekly objective is 90 farrowings per week, I would go for two rooms that could house 48 animals per week. For me it is important to be able to consider weaning twice a week if necessary. If I only have one room per week it would not be possible to do so without breaking the All In- All Out principle. I don´t like splitting the weekly batch in many rooms, as it is not very convenient from a work optimisation point of view.”
Corchón is also in favour of splitting the weekly batch in two: “I don´t like rooms of more than 40 crates. For me the ideal room would have 40 pens, a central passage with 20 farrowing pens on each side.
Farrowing house design
One of the key areas is the layout of the farrowing crate: should sows be placed facing the wall or the passage?
Of course, if the sow is facing the wall and the passage is behind its back (figure 1), monitoring the farrowing and providing assistance if needed becomes easier. Work will be safer and more comfortable, and the crates will also be easier to clean. On the contrary, to access the trough we have to enter the pen every time, which it is more time consuming and it increases the risk of spreading diseases.
Lorente favours, without a doubt, the rear or a double passage. The feeding system in place will determine our decision. If the feeding system is automatic (for example liquid feeding or an electronic dispenser with intake control), allowing for the control of the feeding from the rear passage, Lorente would place the sows facing the wall, without the need for a front passage. But in more manual systems, or those that need to be constantly adjusted (dispensers), a double passage is necessary (figure 2), in order to have an easier access to the trough.
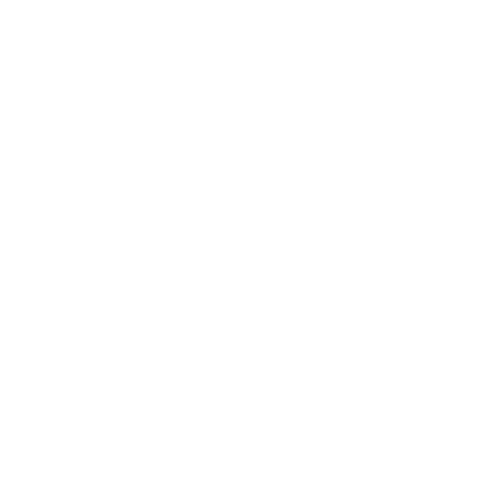
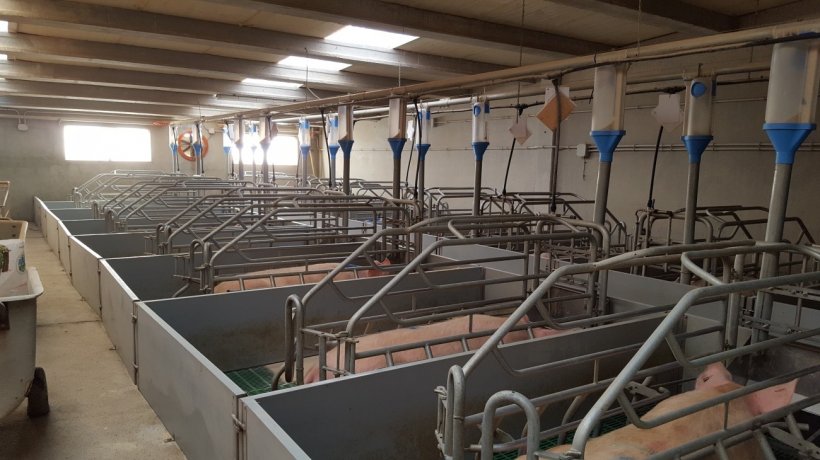
Figure 2. The cost of a farrowing room with a double passage is a 10% higher, but it simplifies work because it provides good access to the feed trough and the rear of the farrowing pen.
For Corchón, placing the sow facing the wall has some advantages: you have a better view of the trough, the sow can be checked more easily from behind, and even, from a construction point of view, the crate is more securely fixed. Though scarcely used in many countries, he would go for the double passage, the main one behind the sow (0,9-1m wide), and a narrower one (0,6m) in front that would allow access to clean the trough, etc. This option of the double passage increases the construction price by approximately 10%.
In addition, both of them clearly support the option of piglet shelter areas (figure 3), and that would require a rear passage to observe the piglets in the creep area. The creep areas provide a good environment for the piglets and, at the same time, keep the farrowing rooms at the right temperature for the sows (19-21 ºC).
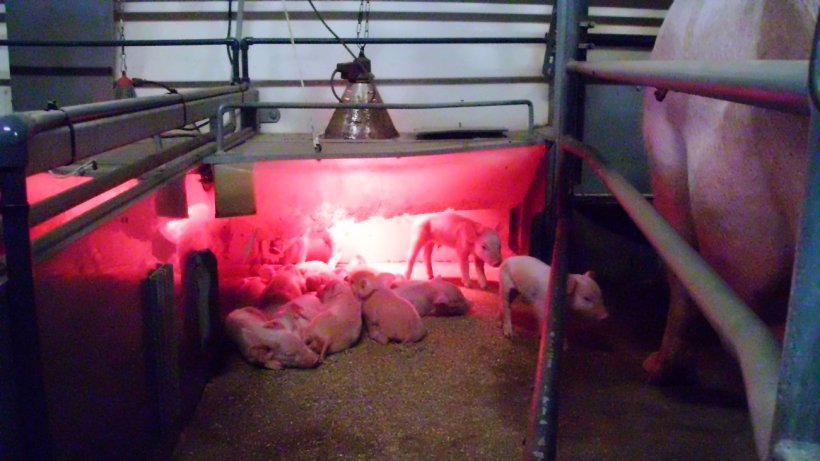
Figure 3. The temperature requirements of the piglet and the sow are completely different. The creep area allows us to give the right comfort to the piglets without compromising the comfort of the sow.
Type of crate
There are many different options. Corchón prefers crates with fingers (figure 4) that prevent the protection rail from covering the udder. He says: “it is true that floating bottom rail can be moved to avoid it completely covering the upper row of teats but, based in farm experience, it is better to make things easy, because the staff do not always adjusts the height of the rail to the teat height of the sow”. On the contrary, Lorente prefers the bottom rail (figure 5) because, in his opinion, the fingers can take up the room of a piglet, which, considering the large size of current litters, should be avoided if at all possible.
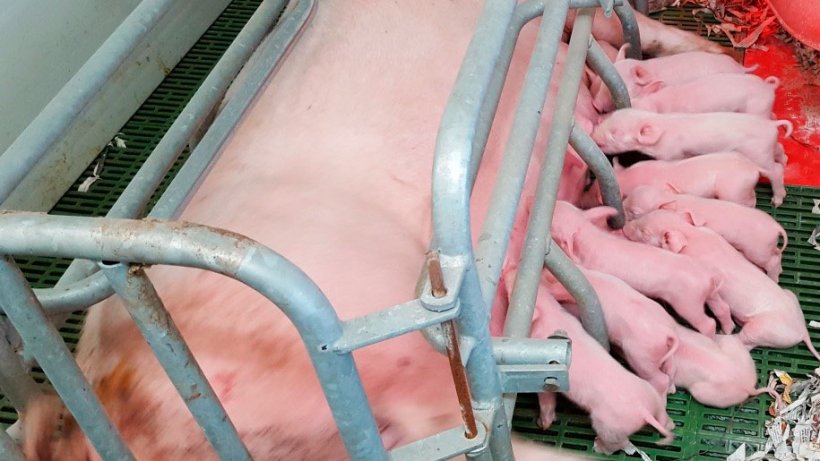
Figure 4. Crate with fingers and a floating rail. The floating rail is a very efficient system to prevent piglets from being laid on. The purpose of the fingers is to facilitate access to the sow udder.
Lorente insists on the importance of the floating internal rail to avoid piglets being crushed: “it is essential to prevent the sow from lying suddenly on the piglets. In modern feeding systems where we aim for a high feed intake during lactation with multiple meals per day, this rail is essential. Without it, the risk of the sow lying down on her piglets would increase exponentially.”
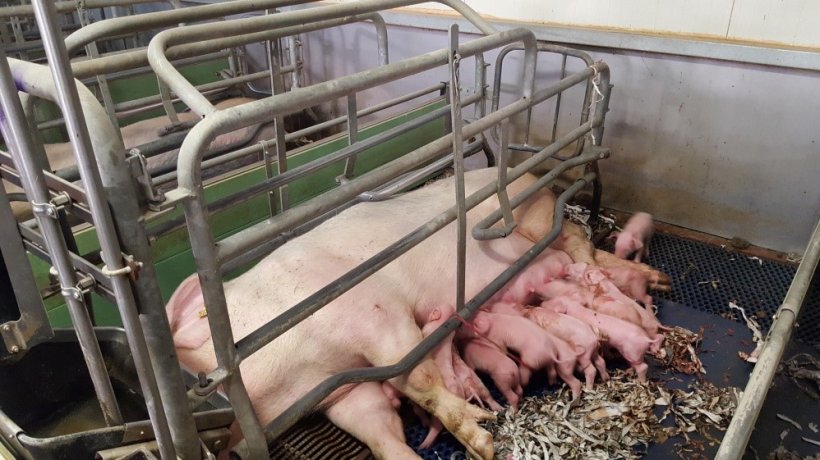
Figure 5. Adjustable rails are more comfortable for the sows because they offer a greater width for them to lie down and nurse their piglets. Despite this, proper adjustment is essential, so that they do not cover a complete row of teats.
Crate and heat mat dimensions
Corchón has some doubts: “the standard dimensions used in current production systems are 1.80 m wide by 2.60 m long. These will probably be increased to 1.90 × 2.60 m in a short time, but I personally would not rush to make them so wide myself. Some questions regarding production still need to be answered before taking this step.”
Lorente agrees with this view, but points out that “we must not forget to increase the size of the heat mats (in case we use them) or the size of the creep area for the piglets. If we are working with hyperprolific sows the area must be, at least, 1.2 × 0.5 m; the old dimensions, 1.2 × 0.4, are not enough “ (figure 6).
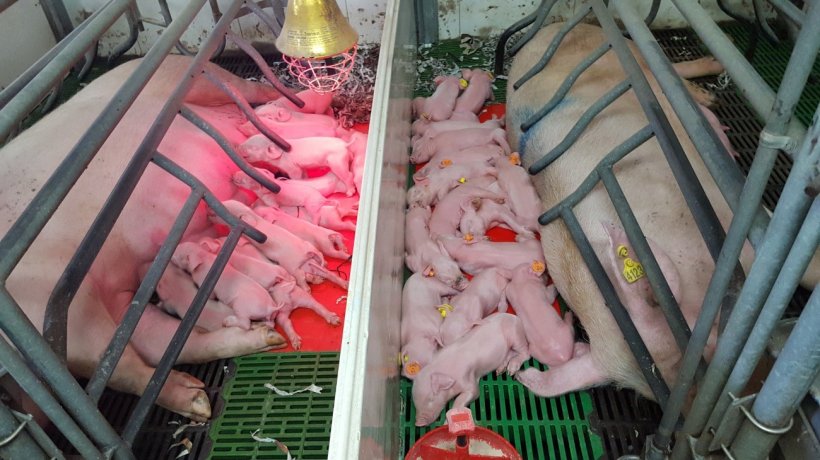
Figure 6. Narrow farrowing pens or narrow heat mats must not be used with hyperprolific sows. This way we will prevent high mortality due to piglets being laid on.
In our next article, Heraclio Corchón and Javier Lorente talk about the type of floor, ventilation, heating, and a crucial area such as the type of feeding system.