Compound feed manufacturing is a key process in swine production, where uniformity and mixing quality play a fundamental role in the success of both the feed mill and the farm.
The proper mixing process ensures uniform nutrient distribution and directly impacts production performance, animal health and welfare, and economic efficiency.
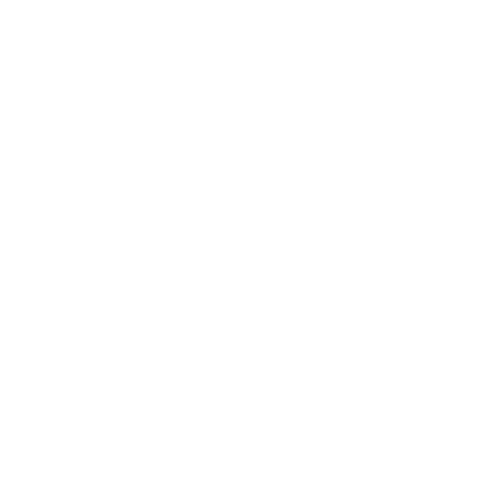
Poor mixing can compromise feed efficiency, affecting the profitability of swine production. This article explores the factors that influence the mixing process and its impact on both the feed mill and the farm.
The quality of swine feed starts with the proper formulation of the diet, which should meet the animal's nutritional needs at each stage of its life. However, inadequate mixing can compromise the efficacy of the initial formulation, leading to the segregation of ingredients that affect the digestibility and pig health. On the other hand, homogeneous mixing ensures that each animal receives a constant dose of nutrients, optimizing its health and performance.
The mixing process in the feed mill
The mixing process is one of the most critical in manufacturing compound feed. The main objective is to ensure uniform distribution of all ingredients, from macronutrients (cereals, proteins, minerals, amino acids, and fats) to micronutrients (vitamins, trace minerals, enzymes, and additives). Poor mixing can result in nutritional variations that affect animal health and performance.
Selecting the mixer is fundamental and should be based on the characteristics of the ingredients and the production requirements. The most commonly used are horizontal paddles or ribbon mixers.
- Paddle mixers are ideal for higher viscosity or density ingredients, as they generate more aggressive movement that facilitates homogeneous incorporation.
- Ribbon mixers are more suitable for lower-density materials.
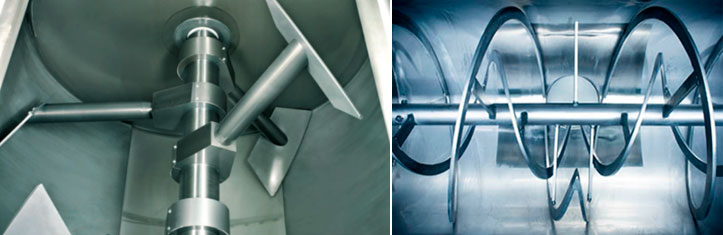
Figure 1. On the left is a horizontal single-shaft paddle mixer (Picture: Buhler AG catalog). On the right is a ribbon mixer (Picture: Flowtec catalog).
Mixing time is a key factor in ensuring feed uniformity. Insufficient mixing time can lead to uneven ingredient distribution, compromising the quality of the final product. On the other hand, excessive mixing time can degrade the structure of the ingredients and affect their nutritional properties.
It is essential to precisely control both the mixing time and conditions to ensure homogeneous mixing, especially considering that these parameters may vary according to feed composition.
Groesbeck et al. (2007) conducted a study to evaluate how mixing time influences feed uniformity. By analyzing crude protein in feeds mixed for different times, they found that an increase in mixing time improved the uniform distribution of protein.
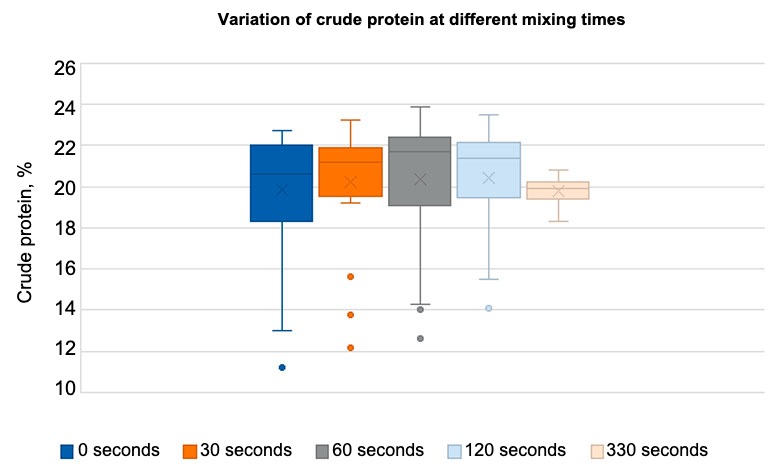
Graph 1. Variation of crude protein in feed mixed for 0, 30, 60, 120, and 330 seconds, respectively. It can be observed that the dispersion is lower when mixing for 330 seconds. Adapted from Groesbeck et al., 2007.
Following the same line of research, Rocha et al. (2022) evaluated the effect of mixing time on the coefficient of variation of chicken feed. The analysis was carried out using microtracers as an evaluation tool. The results obtained are presented in the table below.
Table 1. The effect of mixing time (30, 60, 90, and 120 seconds) on the coefficient of variation of chicken feed, where it is observed that the longer the mixing time, the lower the coefficient of variation. Adapted from Rocha et al., 2022.
Feeds | ||||
---|---|---|---|---|
Treatment | Phase 1 CV (%) |
Phase 2 CV (%) |
Phase 3 CV (%) |
Phase 4 CV (%) |
30s | 35.90 | 49.50 | 34.80 | 40.80 |
60s | 20.40 | 22.60 | 11.90 | 10.00 |
90s | 10.70 | 8.90 | 9.80 | 10.80 |
120s | 7.50 | 5.40 | 5.40 | 5.80 |
P-Linear | <0.0001 | <0.0001 | <0.0001 | <0.0001 |
P-Squared | <0.0001 | <0.0001 | <0.0001 | <0.0001 |
Impacts of mixing on animals
A well-mixed feed ensures that pigs receive a consistent distribution of nutrients in each portion, which supports key performance indicators such as average daily gain (ADG), average daily feed intake (ADFI), and the feed conversion ratio (FCR). These effects directly impact animal growth and nutrient use efficiency, as demonstrated by the results of Groesbeck et al. (2007).
Table 2. Effect of mixing time on piglet performance. Feeds were mixed for 0, 30, 60, 120, and 330 seconds, respectively. Adapted from Groesbeck et al., 2007
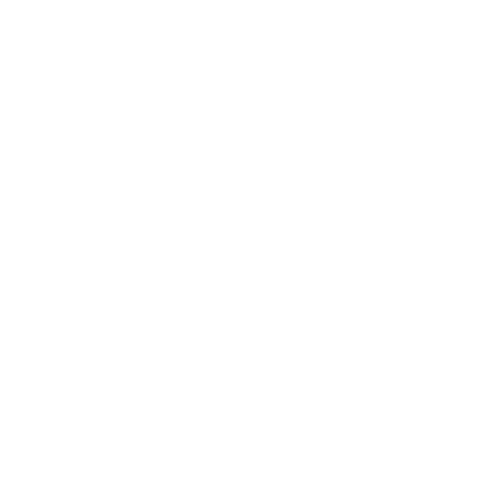
Mixing time | ||||||||
---|---|---|---|---|---|---|---|---|
0s | 30s | 60s | 120s | 330s | SE | Linear P-value | P-squared value | |
0-14 days of life | ||||||||
Initial weight, kg | 6.30 | 6.30 | 6.30 | 6.30 | 6.30 | 0.16 | 0.42 | 0.65 |
ADG, g | 190.00 | 249.00 | 245.00 | 256.00 | 280.00 | 23.25 | 0.01 | 0.10 |
ADFI, g | 253.00 | 298.00 | 275.00 | 292.00 | 314.00 | 19.04 | 0.03 | 0.49 |
FCR | 1.33 | 1.20 | 1.12 | 1.14 | 1.12 | 0.05 | 0.03 | 0.03 |
14-28 days of life | ||||||||
ADG, g | 473.00 | 562.00 | 569.00 | 595.00 | 646.00 | 48.50 | 0.01 | 0.12 |
ADFI, g | 687.00 | 822.00 | 793.00 | 841.00 | 889.00 | 56.14 | 0.01 | 0.17 |
FCR | 1.45 | 1.46 | 1.39 | 1.41 | 1.38 | 0.03 | 0.11 | 0.32 |
0-28 days of life | ||||||||
ADG, g | 331.00 | 405.00 | 407.00 | 426.00 | 463.00 | 35.04 | 0.01 | 0.01 |
ADFI, g | 470.00 | 560.00 | 534.00 | 566.00 | 601.00 | 35.89 | 0.01 | 0.19 |
FCR | 1.42 | 1.38 | 1.31 | 1.33 | 1.30 | 0.03 | 0.04 | 0.10 |
Final weight, kg | 15.60 | 17.60 | 17.70 | 18.30 | 19.30 | 1.20 | 0.01 | 0.89 |
SE = Standard error.
The connection between the feed mill and the farm
The impact of an efficient mixing process goes beyond the feed mill; it is directly reflected on the farm. A well-mixed feed improves pig productivity, optimizing farm profitability. Therefore, it is critical that the feed mill is in constant communication with the farm to adjust for any deviations that may be observed.
Something to consider with feed in meal form is the distance between the feed mill and the farm. Long-distance transport can affect feed uniformity since vibration promotes demixing, which is aggravated when there are very different particle sizes.
Conclusion
The uniformity and quality of swine feed mixing are crucial for the productive performance, health, and welfare of the animals and for the economic efficiency of production. Proper mixing ensures that animals receive a balanced and nutritionally adequate diet, which promotes growth and performance. Conversely, poor mixing can cause nutritional imbalances, health problems, and higher operating costs. Investing in efficient mixing technologies, training personnel, and constantly monitoring process quality is essential to ensure sustainability and profitability at both the feed mill and farm levels.
Recommendations for optimum mixing
- Select suitable equipment: Choosing a mixer that is suitable for the type of ingredients and size of the operation is crucial. Mixers should ideally be stainless steel, easy to clean, and maintained in good condition to ensure not only homogeneous mixing, but also feed security and safety.
- Particle size of raw materials: Ingredients should have as uniform particle sizes as possible. Significant differences in particle size hinder homogeneous mixing and affect feed quality.
- Continuous monitoring: It is important to constantly monitor the mixing process, using tools such as microtracers or micro minerals to evaluate homogeneity. This control should be performed at least once a year. The ideal CV is less than or equal to 5%.