We met in China, in the region of Guigang, in the state of Guangxi. Here, in the district of Gangnan, we find the Yangxiang company and its farm of reference: the Guifei Mountain Sow Farm.
Biosecurity
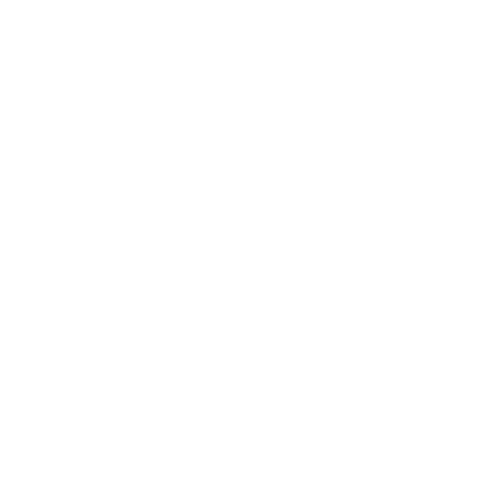
The first aspect that stands out on this farm is its biosecurity at its entrance. If we think that we are talking about a 28,000-sow farm with its future replacements in only 4 buildings, it is not strange. Before entering the farm, one must first spend three days in the company’s headquarters. There they have apartments for the visitors and the employees, and their movements are controlled at all times (photo 1).
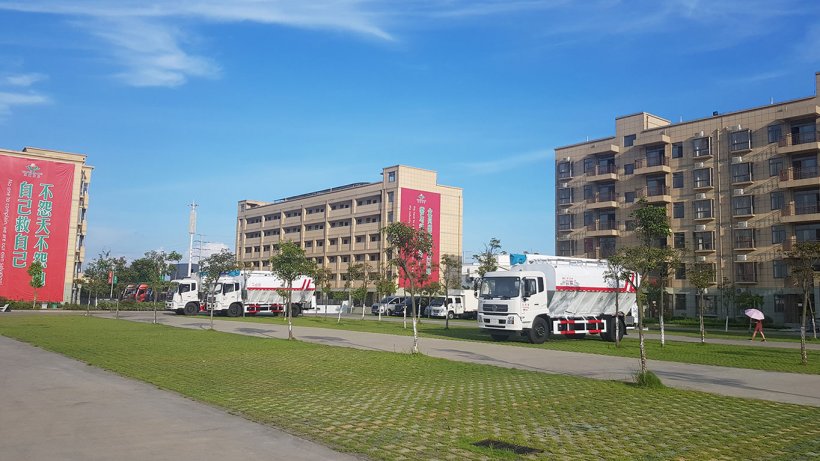
Photo 1: Apartment buildings at the company’s headquarters
After that period of time, people can leave, with clothing provided by the company and in internal vehicles (cleaned and thermally disinfected) towards the mountainous area where the farm is located. When we reached the road leading to the farm, where only the vehicles that go to or come from the farm circulate, we stopped for some 30 minutes for a new cleaning with cold water and soap and a subsequent disinfection. Both the vehicles and the drivers are totally managed by the company.
Approximately 1 km after we stopped again for a second cleaning and disinfection of the vehicle, that this time was shorter. It was carried out without soap for some 10 minutes.
We kept on ascending until reaching the great entrance gate where we had to get off the car, wash our hands, put a first protective overalls on and get on a new internal car that took us to the next level.
From this point on, only the access of lorries that are going to load animals or take raw materials to the exclusive feed mill is allowed. But before reaching the loading or unloading area there is a new cleaning and thermal disinfection point through which all the lorries go through. From here, a complete fence surrounds completely the area where the animals are housed.
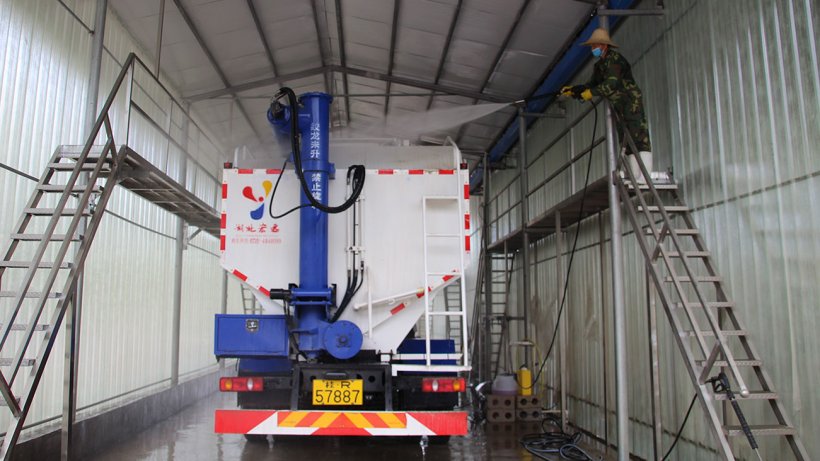
Photo 2: Cleaning centre located at the entry point.
Once loaded with animals, the vehicles never exit the area through the aforementioned road, but through a specific exit road.
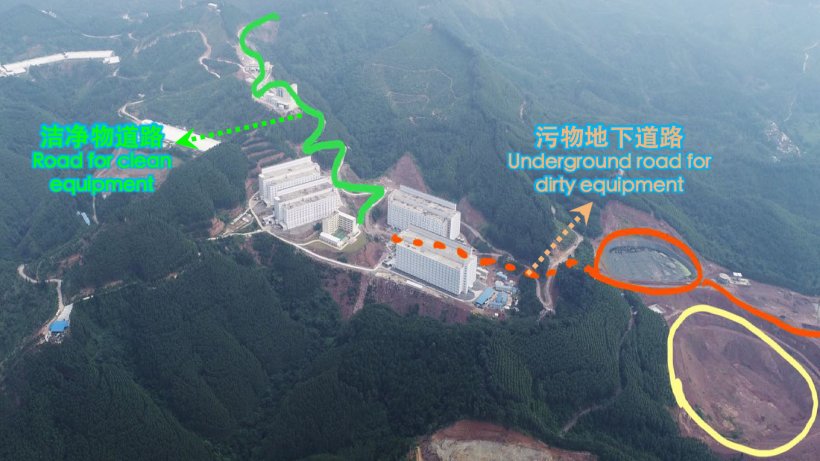
Photo 3: Access and exit road to and from the area where the animals are housed.
When carrying out the visit, they were building a raw material transportation hub so these lorries will not enter the next level.
Once this point is reached, anyone who is going to enter the farm must go through a new 2-night quarantine and, of course, go through a whole area of showers and a disinfection system.
Any material that must enter the internal area goes through a cleaning, disinfection and quarantine process before it can be used.
In this drawing we can see the different security levels (colours) and the movements that must be carried out between them.
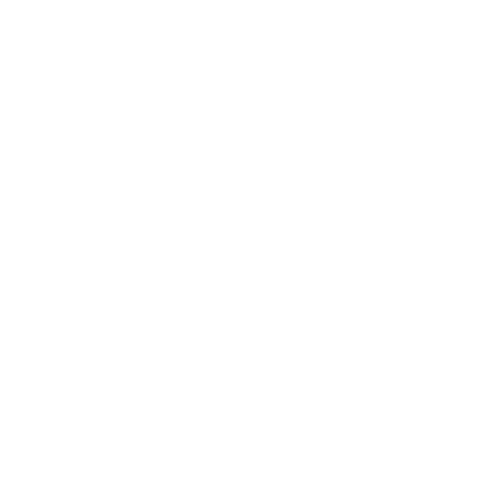
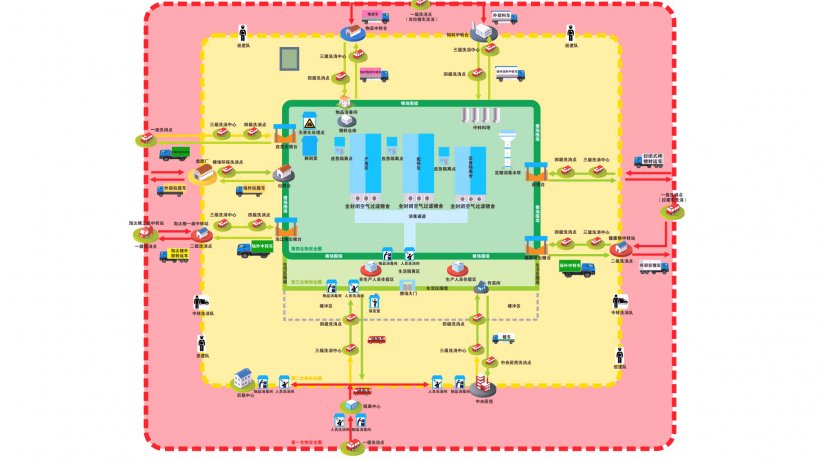
Photo 4: Security levels
Description of the farm
The complex, that includes the “multi-storey” building, is very large and is constantly growing. We will focus on the main current production nucleus, so we can get an idea.
Each of the buildings has been planned to work totally independently. The first two that were built have 7 floors each. Of them, 6 floors are designed to house 1,086 sows per floor and the rest work as the nursery and the area where the future own replacement gilts are raised. The rest of the piglets are removed from the farm at weaning. The last two buildings built have 9 floors each, and 7 of them house 1,086 sows each and the other 2 house the future breeding females.
If we make a quick calculation we are talking of two buildings with a capacity for 6,500 sows each and another two buildings that can house 7,600 sows each. A total of 28,000 sows with an estimated total production of 13,575 piglets per week.
The Pig Business Unit’s CEO, Mr. Liu, tells us that in every floor there are 5 exclusive workers, so the 7-storey buildings have 35 workers in total, and the 9-storey buildings 45. All the workers in the complex remain in it for 3 whole months after having passed the quarantine processes, and they work 6 days a week and rest one. In this way, the number of movements of entry and exit of people is reduced as much as possible.
The farm had its first weanings on January 2nd, 2018, and in May 2019 the first litters were born in the 9-storey buildings. Its technical manager told us that this farm’s goal is to produce animals with a high genetic value and health to sell gilts to a great number of producers and companies.
To provide feed to all this complex, a feed mill was built that can produce 4,680 tonnes a month.
Production data
The farm’s current production data in the two 7-storey building, that are already working to their full capacity (units 3 and 4 for them) and the mid-term goals are:
Unit 3 | Unit 4 | Goal | |
---|---|---|---|
Farrowing rate (%) | 79.83 | 82.56 | 88 |
Total born | 13.49 | 13.63 | 13.5 |
Total born alive | 12.68 | 12.66 | 12.5 |
Weaned per farrowing | 11.52 | 11.08 | 11.8 |
Piglets weaned/sow/year | 26.50 | 25.46 | 27.14 |
Weight at weaning | 7.31 | 7.01 | 7.8 |
Days of lactation | 25.77 | 25.65 | 28 |
Kgs weaned per sow and year | 193.70 | 178.50 | 211.70 |
General management of the farm
We went deeper into the management of the farm and Mr. Liu told us that, currently, they are not able to produce all the replacements needed on the farm, because they are growing, but that the goal is to do it as soon as possible to minimise the risk entailed by the entry of animals.
All the farm has a very advanced climate control system with air filtration, air conditioning and negative air pressure. This ventilation is carried out through the floor of each of the stories, and the extraction is carried out through chimneys that take the air to the top of the building, where there is a system for cleaning the air with water to reduce the odors.
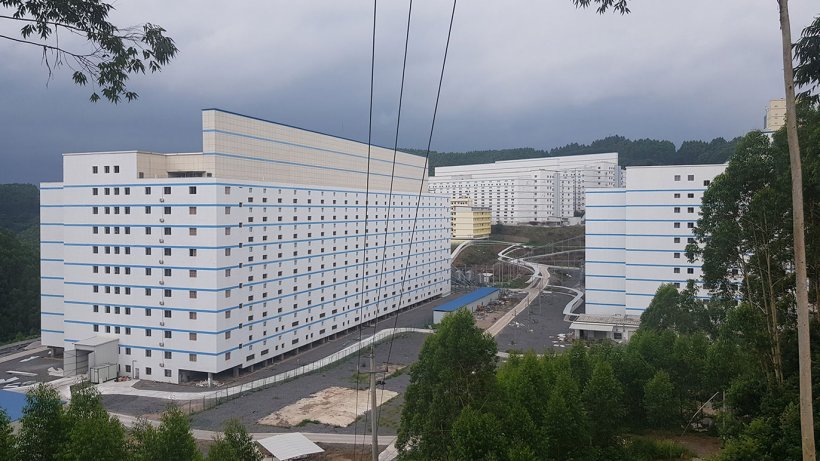
Photo 5: Here we can see the transverse chimney for the exit of the air.
It is important to understand that each floor works as an independent farm. This is, in each floor there are the gestation and farrowing areas, and therefore the sows do not have to be taken from one floor to another one, and the only movement between them is for entering gilts or move the breeding weaner gilts, after their weaning, to the floor where they will be reared. Once weaned, the piglets are taken to a lift that takes them to the ground floor, and from here to the loading dock, from where they will be taken to the fattening quarters.
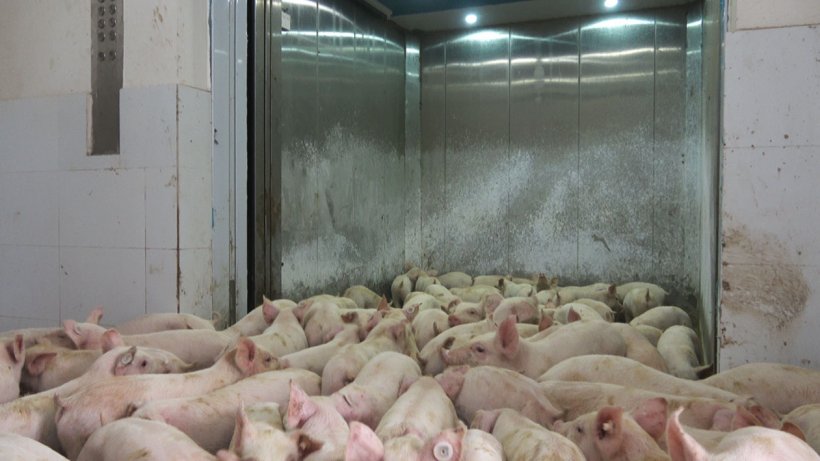
Photo 6: Lift for moving the animals.
The feeding is automated and with dry feed, with a traditional feeding program that feeds once a day in gestation and three times a day in the farrowing quarters to improve the sows’ feed consumption.
The feeding system, designed, built and put in operation by a Danish company is, without a doubt, another of the aspects that we must highlight at the Guifei Mountain Sow Farm. To maximise biosecurity and to avoid the entry of vehicles into the facility, a complex feed distribution system has been designed that goes from the feed mill to the ground floor of each of the buildings (photo 7). From there, an even more sophisticated mechanical impulsion system, through a chain system, lifts the feed to each of the floors (photo 8).
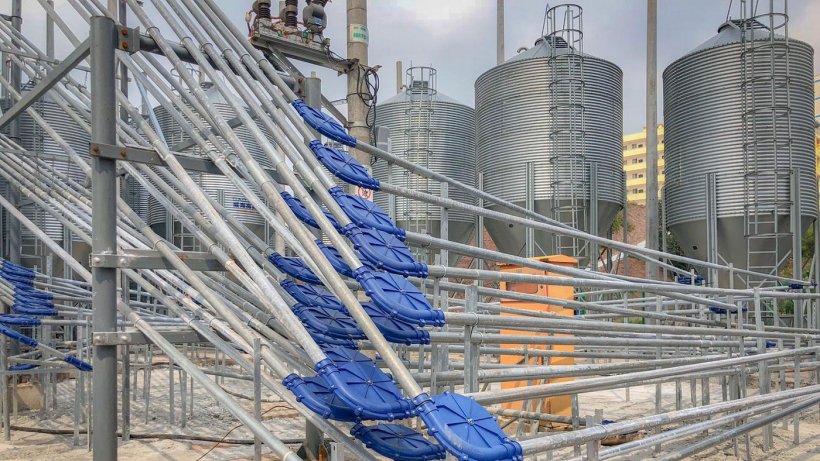
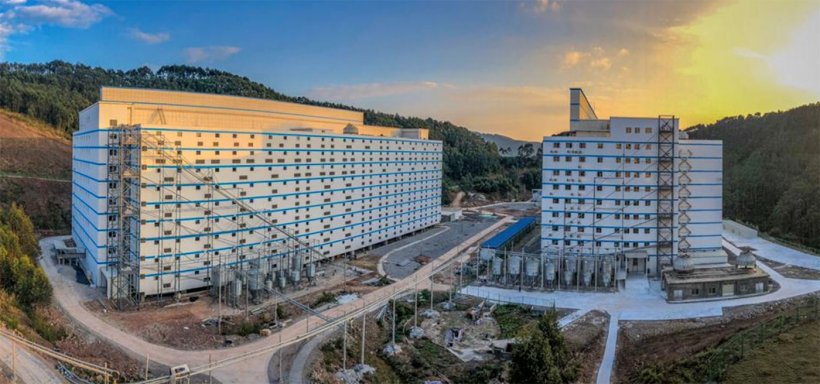
Photo 8: Distribution of feed from the ground floor to each of the floors.
All the units already work with group-housed sows during their pregnancy, insemination in stalls and their transfer to the group housing at 5 weeks, although they tell us how they have evolved in this sense, going from “walk-in, lock-in” stalls in the first two buildings to electronic feeding systems with transponders in the 9-storey buildings.
The temperature management of the piglets is carried out with electric heat mats without nests, and to this date, tail-docking is still performed in all the piglets, but the company wishes to stop doing it in the future, although without a clear date.
Another of the aspects that undoubtedly catch the eye is the management of the dead animals. To take care of this, a sanitation system was designed that allows to remove the dead animals down a chute that take them to the ground floor, where they are introduced into an incineration system present in each of the buildings.

Photo 9: Sanitation system for the dead animals.
We had the chance to meet with the owner of the company and talk in depth about its origin and evolution. We will see it in another article.