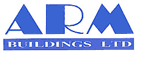
As a result it can cause particular problems for pig producers in both summer and winter. Under the traditional continuous-stocking systems small pigs were added to a house when heavier ones went off for slaughter. Now, whole houses tend to be cleared within two or three weeks. If whole batches of young pigs are introduced in the depths of winter, they can be very cold unless the minimum ventilation rate is accurately controlled or supplementary heating is employed.
“At this stage the average bodyweight in the house is low compared with a continuously-stocked building,” points out Tim. “Conversely, when all the pigs are near the finishing stage, then the average liveweight is high and the heat output can be enormous.”
He points out that a finishing pig produces about 200 watts of heat. “In a building with 200 pigs this is equivalent to forty 1kW electric fires —a lot of heat for the ventilation system to extract, particularly in hot weather if an old building’s insulation is not enough to keep out the heat from the sun.”
This problem, he says, has been exacerbated by the increase in average finishing weight. Defra figures show that, over the last 10 years, the average carcase weight of finished pigs in the UK has risen from 69.2 kg to 78.5 kg — that’s nearly 10 kg over the decade. This equates to a liveweight increase of around 15 kg. The knock-on effects of this are now being felt on many farms, he says.
He advises producers with older buildings to have their ventilation systems professionally checked. “Batch systems would require around 30 per cent more fan capacity than the same building using continuous stocking due to the higher average bodyweight of the pigs,” he said.
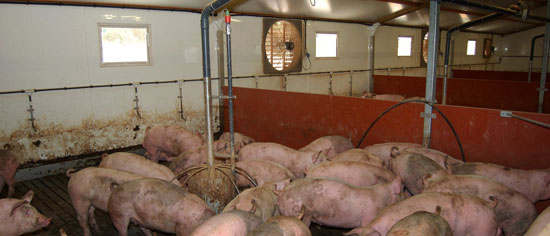
Batch production systems and higher slaughter weights mean piggeries need accurate control of ventilation to avoid large fluctuation in temperature, says Tim Miller
www.armbuildings.co.uk