A new sow complex is now under construction featuring the first prefabricated steel swine barns in the United States. Compared to traditional wood structures, the steel buildings are designed to offer a more biosecure, flame-retardant and energy-efficient environment for pigs, while also being more durable and faster to build.
The 12,000-head sow facility is scheduled for completion this summer in South Dakota. The steel building package, designed by C-Lines, is being provided by AP, AGCO’s swine equipment brand. AP dealer Ag Property Solutions is constructing the barns, which will be managed by Pipestone Management.
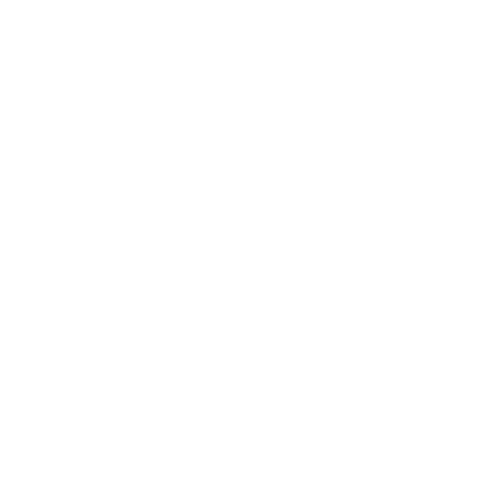
Two swine buildings at the site will utilize polyisocyanurate (PIR) insulated plasterboard sandwiched between two sheets of metal in their sidewalls and ceilings. With high thermal performance, the foam can smolder and melt but will not burn or drip, nor cause surrounding materials to catch fire.
Other benefits include:
Construction speed and efficiency – Wood structures require a massive amount of lumber, especially in the trusses and attic, and take time to construct. The C-Lines fully bolted steel structures are prefabricated and arrive on the construction site ready to bolt together for a faster and cleaner construction process.
Building strength – The galvanized steel frame offers durability, strength and corrosion protection not found in wood frame construction. The lighter weight and strong load-bearing capacity allow for larger roof spans, a lower profile roof and post-free production spaces. Perfectly smooth inner walls and ceilings offer easy cleaning and uninterrupted ventilation and rust apparition compared to corrugated walls and ceilings. A stronger ceiling allows employees to walk the attic to inspect and maintain filtering systems.
Energy efficiency – The PIR insulated metal panels, ranging from 1.5 to 4 inches in thickness, can meet specific energy efficiency requirements ranging from R12 to R30. The solid core polyurethane foam provides enhanced insulating characteristics compared to wood structures and a tighter barn seal for enhanced filtration and animal comfort.
Biosecurity – The insulated metal panels eliminate the use of cellulose in the attic space, which is a common harbor for bugs and bacteria. In addition, insulating foam is resistant to moisture, helping to keep the barn environment comfortable for pigs.
Easily transportable – Prefabrication allows structural parts to be easily transported in bundles to any project location by truck or containers.
In addition to manufacturing the building components, AP will provide its technology-advanced swine production equipment, including feed and ventilation systems, bin scales and EDGE 2 controller.
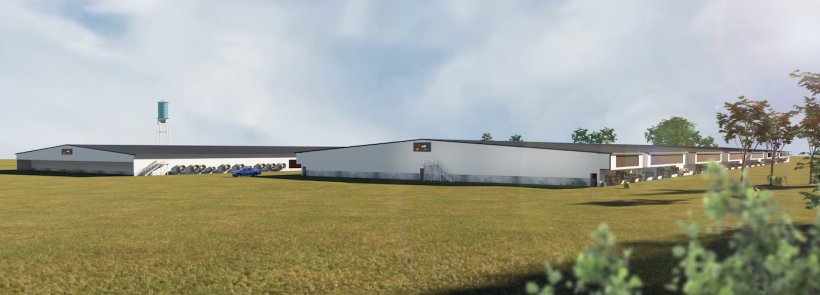
Massive scope
The new facility is the largest sow complex ever constructed by Ag Property Solutions, with a footprint of up to 55 acres. It includes a 187,500-square-foot farrowing barn and gilt developer unit and a 225,000-square-foot gestation barn that incorporate the steel panels. The site will also have a compost structure and tractor shed both made from wood.
When fully operational, the facility will utilize in excess of 20,000 tons of feed per year and 60,000 gallons of water per day and produce over 45 million pounds of retail pork cuts per year.
Chris Schmitz, director of construction services for Ag Property Solutions, said APS discussed the idea of a wood alternative swine structure with Pipestone Management for several years. “With insurance premiums on the rise, catastrophic fire concerns and biosecurity threats, 2022 was time to make it a reality,” he said. “Last summer, forces aligned with AP presenting a steel building package option for our turnkey construction bid.
He noted that the all-steel barns entail higher building material and labor costs compared to wood structures, but they will ultimately provide an insurance expense payback after a period of time which will vary depending on the facility.
January 25, 2022 - Ag Property Solutions