“Success in the piggery doesn’t depend upon the equipment but on the people using that equipment. Management needs to recognise its own ignorance. Monitoring piggeries has exposed much ignorance about the environment in which we keep our pigs, but it has also indicated simple ways to improve it — and save costs at the same time,” Hugh Crabtree, managing director of Farmex told a meeting of the Fosseway Pig Discussion Group at Leadenham, Lincolnshire.
He pointed out that while there was no need to measure everything, monitoring key factors such as temperature, water flow, electricity and feed supply augers, could have a huge effect.
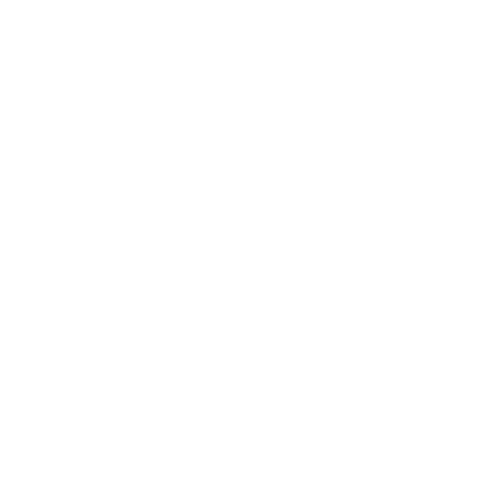
For instance, monitoring the temperature in flat-deck rooms in a Suffolk flat-deck, enabled heating costs to be reduced from £1.27 per pig to just 41p, giving an annual saving of £8,877, through better management of ventilation rate.
Another practical example came from ARM Buildings who install monitoring equipment in their finishing houses as standard. BPEX figures showed that the electricity use was 16 kWh per finished pig, costing £1.41, compared with an industry average of 40kWh per pig, costing £3.52.
But Hugh Crabtree warned that information provided by monitoring should be used to change old habits which were not necessarily based on factual information.
Monitoring should be used as a useful management tool. A drop in feed or water consumption could predict an outbreak of disease allowing early intervention. This has been shown to save thousand of pounds on large-scale units.
“You can’t control what you don’t measure and monitoring has shown that the greatest variable on any unit is not the pigs or the equipment — but the human being!” -
3 November 2011 - Farmex (Farm Energy & Control Services Ltd)